Rotary kiln
A rotary kiln and rotary kiln technology, applied in the field of rotary kiln, can solve the problems of large kiln body area, low thermal efficiency, and ceramsite products are easy to break, so as to reduce the occupied area, increase the heat exchange area, and reduce the length Effect
- Summary
- Abstract
- Description
- Claims
- Application Information
AI Technical Summary
Problems solved by technology
Method used
Image
Examples
Embodiment Construction
[0017] The present invention will be further explained below through non-limiting embodiments in conjunction with the accompanying drawings:
[0018] As shown in the figure, a rotary kiln includes a rotary kiln barrel 4, a kiln head 1, a kiln tail 8, and a transmission device that drives the rotary kiln barrel 4 to rotate. The kiln head 1 is set on the rotary kiln barrel through a sealing device 2 The head of 4 and the kiln tail 8 are set at the tail of the rotary kiln cylinder 4 through the sealing device 2. The rotary kiln shell 4 is inclinedly arranged, and the kiln tail 8 is higher than the kiln head 1. The two ends of the rotary kiln cylinder 4 are respectively supported by supporting rollers 9 arranged at the lower part of the rotary kiln cylinder 4. The rotary kiln cylinder 4 is covered with a tire belt 3 at a position corresponding to the supporting roller 9, and the supporting roller 9 is in contact with the tire belt 3. The transmission device for driving the rotary ki...
PUM
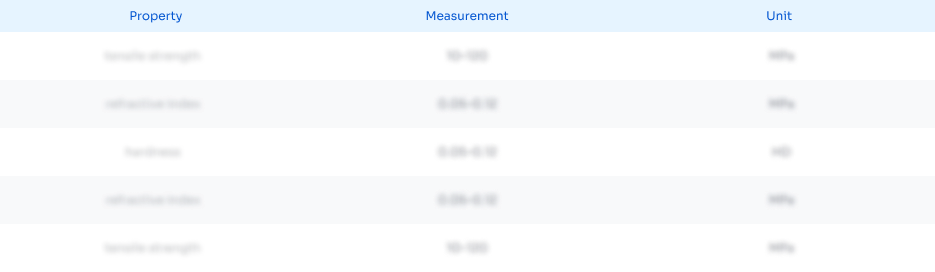
Abstract
Description
Claims
Application Information

- R&D
- Intellectual Property
- Life Sciences
- Materials
- Tech Scout
- Unparalleled Data Quality
- Higher Quality Content
- 60% Fewer Hallucinations
Browse by: Latest US Patents, China's latest patents, Technical Efficacy Thesaurus, Application Domain, Technology Topic, Popular Technical Reports.
© 2025 PatSnap. All rights reserved.Legal|Privacy policy|Modern Slavery Act Transparency Statement|Sitemap|About US| Contact US: help@patsnap.com