Oil temperature control system of forming machine
A control system and oil temperature technology, applied in the direction of presses, manufacturing tools, etc., can solve the problems of lack of cooling oil state and temperature, difficult detection of built-in cooling system, frequent inspection and detection of oil temperature data, etc., to achieve automatic operation , Reduce operating costs, facilitate maintenance and maintenance
- Summary
- Abstract
- Description
- Claims
- Application Information
AI Technical Summary
Problems solved by technology
Method used
Image
Examples
Embodiment Construction
[0021] The present invention will be further described below in conjunction with the accompanying drawings and specific embodiments.
[0022] like Figure 1-Figure 2 As shown, a molding machine oil temperature control system of the present invention includes an oil tank 1 containing drawing oil, and an oil temperature cooling device 2 is installed outside the oil tank 1, and the oil temperature cooling device 2 includes an oil circulation pipe One end of the oil circulation pipeline 21 communicates with the oil tank 1, a gear pump 22 and a first control valve 23 are installed on the oil circulation pipeline 21, and the gear pump 22 is installed on the first control valve 23 The front end of the first control valve 23 is also equipped with a cooler 24, and the other end of the oil circulation line 21 passes through the cooler 24 and communicates with the oil tank 1 to form a circuit; on the cooler 24 The water inlet pipe 25 and the water outlet pipe 26 are respectively connect...
PUM
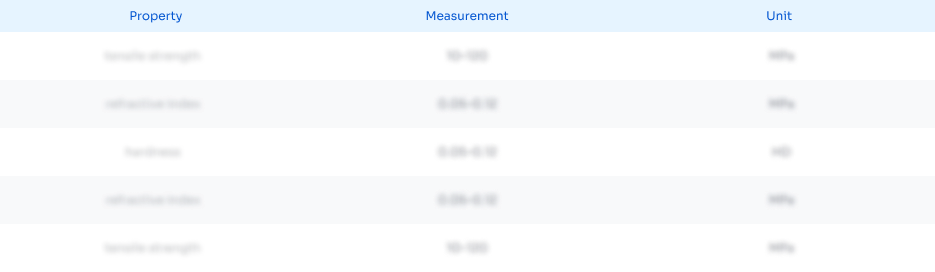
Abstract
Description
Claims
Application Information

- Generate Ideas
- Intellectual Property
- Life Sciences
- Materials
- Tech Scout
- Unparalleled Data Quality
- Higher Quality Content
- 60% Fewer Hallucinations
Browse by: Latest US Patents, China's latest patents, Technical Efficacy Thesaurus, Application Domain, Technology Topic, Popular Technical Reports.
© 2025 PatSnap. All rights reserved.Legal|Privacy policy|Modern Slavery Act Transparency Statement|Sitemap|About US| Contact US: help@patsnap.com