Dual-motor torque synchronization model predictive control method based on quadratic value function
A technology of model predictive control and value function, which is applied in AC motor control, control system, speed regulation of multiple motors, etc. It can solve the problems that the optimal point of control effect cannot be determined, the convergence of error terms cannot be guaranteed, and the weight coefficient cannot be adjusted. , to reduce the computational burden, reduce the complexity of the experiment, and improve the control performance.
- Summary
- Abstract
- Description
- Claims
- Application Information
AI Technical Summary
Problems solved by technology
Method used
Image
Examples
Embodiment Construction
[0048] A quadratic value function dual-motor torque synchronous finite set model predictive control method of the present invention will be described in detail below with reference to the embodiments and the accompanying drawings.
[0049] The object of the present invention is to drive the same heavy-duty dual-motor gear transmission system through two motors. The driving shafts of the two motors are connected with the two driving pinions, the connecting shaft of the load is connected with the driven large gear, and the two pinions are symmetrically distributed The two sides of the large gear are meshed with it, ignoring the elastic connection characteristics of each transmission shaft, and the small gear and the motor connected to it, the large gear and the load connected to it are regarded as a whole, as shown in figure 1 shown. According to the power balance analysis and the transmission ratio between gears, ignoring the friction of the motor itself, the total load torque ...
PUM
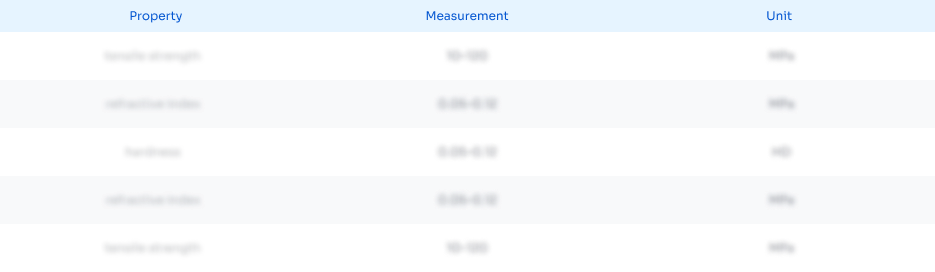
Abstract
Description
Claims
Application Information

- R&D
- Intellectual Property
- Life Sciences
- Materials
- Tech Scout
- Unparalleled Data Quality
- Higher Quality Content
- 60% Fewer Hallucinations
Browse by: Latest US Patents, China's latest patents, Technical Efficacy Thesaurus, Application Domain, Technology Topic, Popular Technical Reports.
© 2025 PatSnap. All rights reserved.Legal|Privacy policy|Modern Slavery Act Transparency Statement|Sitemap|About US| Contact US: help@patsnap.com