A Displacement Control Method of Electro-hydraulic Actuator
An electro-hydraulic actuator and displacement control technology, applied in the direction of servo meter circuit, servo motor components, fluid pressure actuation system components, etc., can solve the problems of not wide application range of temperature, low control accuracy and low control efficiency, etc. Achieve the effect of improving control efficiency, improving control accuracy, and eliminating control errors
- Summary
- Abstract
- Description
- Claims
- Application Information
AI Technical Summary
Problems solved by technology
Method used
Image
Examples
Embodiment 1
[0049] In this embodiment, a displacement control method of an electro-hydraulic actuator is disclosed. The control method is executed after the control signal of the electro-hydraulic actuator controller is in a specific control mode and exceeds a certain amount of variation.
[0050] In this example, if figure 1 As shown, a closed-loop control method of an electro-hydraulic actuator is provided. Since the electro-hydraulic actuator works in a wide temperature range (-20°C to +50°C) and a wide load range (-45000N to +45000N), and requires To meet the positioning requirements of high precision (0.15%), the method is realized through the PID closed-loop control algorithm. Since the PID algorithm needs to collect control signals and feedback signals, this control method needs to be able to collect feedback signals after the electro-hydraulic actuator is running. In this embodiment, the control method provided in this embodiment is executed after the displacement sensor can colle...
Embodiment 2
[0128] In this embodiment, a precision test is carried out on a displacement control method of an electro-hydraulic actuator provided by the present invention, and the test is divided into a normal temperature test and a high and low temperature test.
[0129] Combining the method provided by the present invention with the existing electro-hydraulic actuator, the normal temperature test process is:
[0130] Step 1: Power on the equipment, set the output; power on the electro-hydraulic actuator, and set the control parameters by operating the keyboard, including the control accuracy of 0.03mm;
[0131] Step 2: Set the minimum speed of the motor, the maximum speed of the motor (can not exceed the rated speed); set the parameters such as system position and signal;
[0132] Step 3: Use a standard signal source to simulate the DCS to set the target position, the controller responds to the signal and adjusts the actuator to reach the corresponding position, and records the position...
PUM
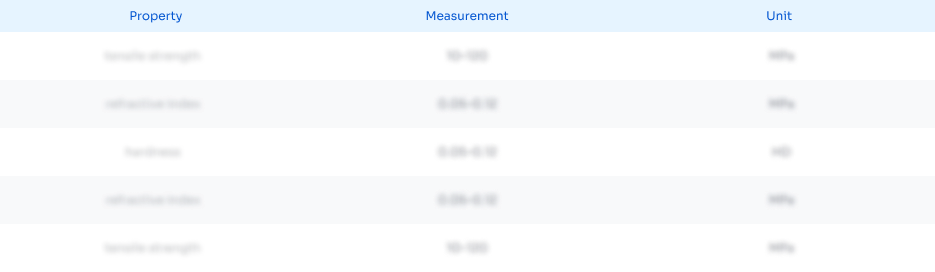
Abstract
Description
Claims
Application Information

- Generate Ideas
- Intellectual Property
- Life Sciences
- Materials
- Tech Scout
- Unparalleled Data Quality
- Higher Quality Content
- 60% Fewer Hallucinations
Browse by: Latest US Patents, China's latest patents, Technical Efficacy Thesaurus, Application Domain, Technology Topic, Popular Technical Reports.
© 2025 PatSnap. All rights reserved.Legal|Privacy policy|Modern Slavery Act Transparency Statement|Sitemap|About US| Contact US: help@patsnap.com