Making process of protective film used for ferrite sintering
A production process, ferrite technology, applied in the field of production process of protective film for ferrite sintering, can solve the problems of increased magnetic sheet loss, long production cycle, inability to disassemble, etc., to improve the pass rate and reduce adhesion rate, the effect of improving production efficiency
- Summary
- Abstract
- Description
- Claims
- Application Information
AI Technical Summary
Problems solved by technology
Method used
Image
Examples
Example Embodiment
[0021] The present invention will be further described below in conjunction with the accompanying drawings:
[0022] In order to make the purpose, technical solutions and advantages of the present invention clearer, the technical solutions in the present invention are described clearly and completely below. Obviously, the described embodiments are part of the embodiments of the present invention, not all of the embodiments. Based on the embodiments of the present invention, all other embodiments obtained by those of ordinary skill in the art without creative efforts shall fall within the protection scope of the present invention.
[0023] A manufacturing process of a protective film for ferrite sintering, comprising the following steps:
[0024] S1. The ferrite powder is made into the green sheet 4 by the casting method or the extrusion method;
[0025] S2. Set the corresponding operating parameters of the laser head in the laser marking machine 1 through the machine operatio...
PUM
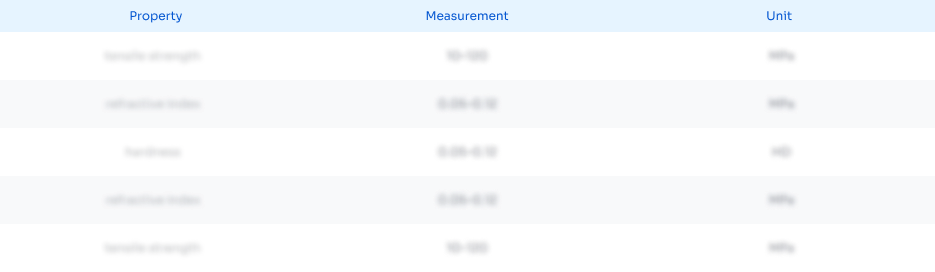
Abstract
Description
Claims
Application Information

- R&D
- Intellectual Property
- Life Sciences
- Materials
- Tech Scout
- Unparalleled Data Quality
- Higher Quality Content
- 60% Fewer Hallucinations
Browse by: Latest US Patents, China's latest patents, Technical Efficacy Thesaurus, Application Domain, Technology Topic, Popular Technical Reports.
© 2025 PatSnap. All rights reserved.Legal|Privacy policy|Modern Slavery Act Transparency Statement|Sitemap|About US| Contact US: help@patsnap.com