Real-time monitoring method in electron beam fuse deposition additive manufacturing
A real-time monitoring and additive manufacturing technology, applied in electron beam welding equipment, manufacturing tools, additive processing, etc., which can solve the problems of long imaging time, low secondary electrons, and reduced production efficiency in the molding process.
- Summary
- Abstract
- Description
- Claims
- Application Information
AI Technical Summary
Problems solved by technology
Method used
Image
Examples
Embodiment Construction
[0053] The electron beam fuse deposition additive manufacturing real-time monitoring method proposed by the method of the present invention comprises the following steps:
[0054] (1) Emit a beam of high-energy electrons on the workpiece to be deposited and added, and the energy of the high-energy electron beam 9 is 10KeV-150KeV, such as figure 1 shown;
[0055] (2) When the deposition starts, the abscissa of the current deposition center of the additive workpiece 3 to be deposited is X c , deflect the high-energy electron beam in step (1), and sequentially scan the preheating area D on the workpiece to be deposited with additives 1 , processing area D 2 and heat treatment area D 3 , and for the preheating region D 1 , processing area D 2 and heat treatment area D 3 The high-energy electron beam current is adjusted according to the following formula:
[0056] Make preheating zone D 1 The high-energy electron beam current I 1 for:
[0057]
[0058] Among them, P 1...
PUM
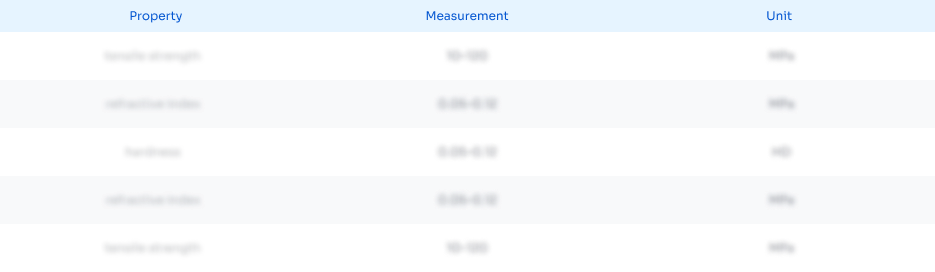
Abstract
Description
Claims
Application Information

- R&D Engineer
- R&D Manager
- IP Professional
- Industry Leading Data Capabilities
- Powerful AI technology
- Patent DNA Extraction
Browse by: Latest US Patents, China's latest patents, Technical Efficacy Thesaurus, Application Domain, Technology Topic, Popular Technical Reports.
© 2024 PatSnap. All rights reserved.Legal|Privacy policy|Modern Slavery Act Transparency Statement|Sitemap|About US| Contact US: help@patsnap.com