An active friction end effector for two-dimensional space friction applications
An end effector and two-dimensional space technology, applied in the direction of manufacturing tools, chucks, manipulators, etc., can solve problems such as capture task failure and equipment damage, and achieve the effect of intelligent capture scheme and high capture efficiency
- Summary
- Abstract
- Description
- Claims
- Application Information
AI Technical Summary
Problems solved by technology
Method used
Image
Examples
Embodiment Construction
[0031] The present invention provides an active friction end effector oriented to the application of two-dimensional space friction. The end effector is used as the end actuator of a space capture robot arm, which can effectively solve the problem of passive derotation capture of non-cooperative targets in spin motion. .
[0032] Such as figure 1 , figure 2 As shown, the active friction end effector for two-dimensional space friction application includes a friction ball 10, a friction ball power device, a friction ball restraint device and a linear modular clutch device; wherein:
[0033] The friction ball power device is used to provide the friction ball 10 with two-dimensional rolling power;
[0034] The friction ball restraint device provides omnidirectional restraint for the friction ball 10 in the free space, and limits the rotation of the friction ball 10 within a certain space range; it is fixedly connected to the end of the space target control mechanism through th...
PUM
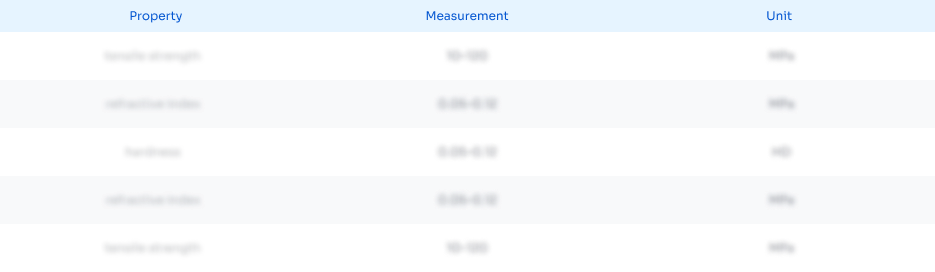
Abstract
Description
Claims
Application Information

- R&D
- Intellectual Property
- Life Sciences
- Materials
- Tech Scout
- Unparalleled Data Quality
- Higher Quality Content
- 60% Fewer Hallucinations
Browse by: Latest US Patents, China's latest patents, Technical Efficacy Thesaurus, Application Domain, Technology Topic, Popular Technical Reports.
© 2025 PatSnap. All rights reserved.Legal|Privacy policy|Modern Slavery Act Transparency Statement|Sitemap|About US| Contact US: help@patsnap.com