Recovering method for ultra-fine-grain ilmenite in inclined plate thickener overflow
A technology of ultra-fine particles and recovery methods, applied in the field of mineral processing engineering, can solve problems such as unsatisfactory recovery of ilmenite, inability to realize efficient use of resources, loss of titanium resources, etc.
- Summary
- Abstract
- Description
- Claims
- Application Information
AI Technical Summary
Problems solved by technology
Method used
Image
Examples
Embodiment 1
[0018] A method for recovering ultra-fine-grained ilmenite in the overflow of an inclined-plate thickener. The raw material to be selected is a fine-grained ilmenite in the overflow of an inclined-plate thickener in Panzhihua, Sichuan, and TiO 2 Grade 15%, -38μm particle size above 95%, such as figure 1 As shown, the specific method is as follows: Concentrate the overflow of the inclined plate thickener to a pulp with a mass percent concentration of solids of 10wt%, and then subject the pulp to high-gradient magnetic separation for three times, one coarse and two fine, and the high gradient magnetic separation used in high-gradient magnetic separation The magnetic gathering medium of the magnetic separator is a rod medium and the diameter of the medium is 1mm. The rough separation magnetic induction intensity is 0.5T, and the magnetic induction intensity of the two selections is 0.3T. The magnetic separation rough concentrate is obtained, and water is added to adjust the rough...
Embodiment 2
[0020] A method for recovering ultra-fine-grained ilmenite in the overflow of an inclined-plate thickener. The ore to be selected is fine-grained ilmenite in the overflow of an inclined-plate thickener in Yunnan, TiO 2 The grade is 10%, and the particle size of -38μm is more than 85%. The specific method is as follows: Concentrate the overflow of the inclined plate thickener to a pulp with a mass percentage of solids of 20wt%, and conduct three high-gradient magnetic separations on the pulp. , the magnetic gathering medium of the high gradient magnetic separator used in high gradient magnetic separation is rod medium and the diameter of the medium is 1.5mm, the magnetic induction intensity of rough selection is 0.6T, and the magnetic induction intensity of the two selections is 0.4T, and the magnetic separation roughness is obtained. Concentrate, add water to adjust the mass percentage concentration of the rough concentrate to 22wt% Flotation desulfurization, flotation desulfu...
Embodiment 3
[0022] A method for recovering ultra-fine-grained ilmenite in the overflow of an inclined-plate thickener. The ore to be selected is fine-grained ilmenite in the overflow of an inclined-plate thickener in Yunnan, TiO 2 The grade is 12%, and the particle size of -38μm is more than 90%. The specific method is as follows: Concentrate the overflow of the inclined plate thickener to a pulp with a solid mass percentage concentration of 15wt%, and conduct three high-gradient magnetic separations on the pulp. , the magnetic gathering medium of the high gradient magnetic separator used in high gradient magnetic separation is a rod medium and the diameter of the medium is 1.8mm. Concentrate, add water to adjust the mass percentage concentration of the rough concentrate to 25wt% to obtain sulfur concentrate by flotation desulfurization, flotation desulfurization is a conventional prior art, add sulfuric acid to the desulfurization tailings to control the pulp pH=6, stir for 4min, and the...
PUM
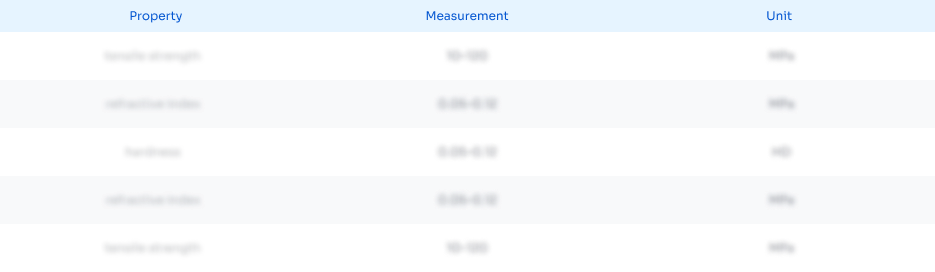
Abstract
Description
Claims
Application Information

- R&D Engineer
- R&D Manager
- IP Professional
- Industry Leading Data Capabilities
- Powerful AI technology
- Patent DNA Extraction
Browse by: Latest US Patents, China's latest patents, Technical Efficacy Thesaurus, Application Domain, Technology Topic, Popular Technical Reports.
© 2024 PatSnap. All rights reserved.Legal|Privacy policy|Modern Slavery Act Transparency Statement|Sitemap|About US| Contact US: help@patsnap.com