An unsteady flow visualization method for an aero-engine compressor
An unsteady flow and aero-engine technology, which is applied in the field of aviation aircraft, can solve problems affecting the authenticity of the flow field, display, and inflexibility, and achieve the effects of reducing labor costs and time costs, improving analysis efficiency, and reducing manual operations
- Summary
- Abstract
- Description
- Claims
- Application Information
AI Technical Summary
Problems solved by technology
Method used
Image
Examples
Embodiment Construction
[0032] A visualization method for the unsteady flow of an aeroengine compressor, such as figure 1 shown, including the following steps:
[0033] Step 1. Use commercial software such as NUMECA or Pointwise to generate multi-block structured grids of single-blade passages of multi-stage compressors. In this way, the amount of grids that need to be generated is small and the generation speed is fast, which greatly reduces tedious manual operations. The computer's memory requirements are also low.
[0034] Step 2. Generate the full-ring mesh of the axial flow compressor through the software SCTMC, take the single-channel mesh as input, and output the full-ring mesh after processing such as rotation and determination of the docking relationship, and mark the compressor blade where each mesh block is located. Row. Since the size of the full-ring grid data file can reach tens of GB, this step can be performed on a supercomputer without manual intervention and without considering th...
PUM
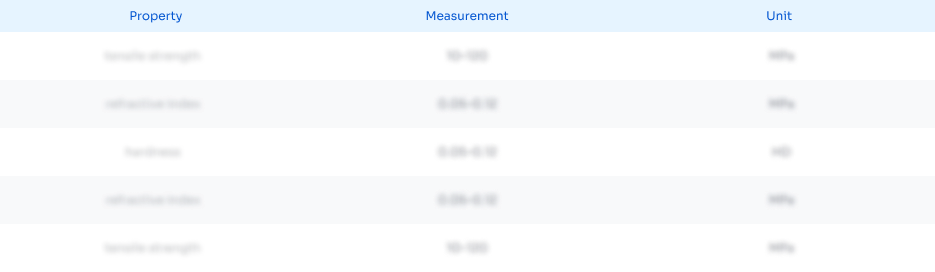
Abstract
Description
Claims
Application Information

- Generate Ideas
- Intellectual Property
- Life Sciences
- Materials
- Tech Scout
- Unparalleled Data Quality
- Higher Quality Content
- 60% Fewer Hallucinations
Browse by: Latest US Patents, China's latest patents, Technical Efficacy Thesaurus, Application Domain, Technology Topic, Popular Technical Reports.
© 2025 PatSnap. All rights reserved.Legal|Privacy policy|Modern Slavery Act Transparency Statement|Sitemap|About US| Contact US: help@patsnap.com