Spinning method for blue fibers dyed through indigo plants
A plant dyeing and fiber technology, applied in the textile field, can solve the problems of fiber bonding and fiber surface roughness, and achieve the effect of reducing the adhesion between fibers, improving the finish, and reducing the generation of static electricity.
- Summary
- Abstract
- Description
- Claims
- Application Information
AI Technical Summary
Problems solved by technology
Method used
Image
Examples
Embodiment 1
[0033] Design and produce white modal and vegetable dyed fiber 50 / 50 14.8tex blended yarn;
[0034] The spinning process designed and adopted is as follows (indicated by machine model)
[0035] Picking cotton (FA002)→opening (FA106)→mixing and opening (FA035)→multi-compartment blending (FA025)→winding (FA076F)→carding (FA226A)→drawing (BHFA1322 one and two)→ Roving (FA493) → spun yarn (TH518) → winding (Murata No.21C-s).
[0036] The specific process parameters are as follows:
[0037] Opening and cleaning: dry weight 380g / m, mixed moisture regain 11%, lap weight 421.8g / m, lap weight net weight 18.06kg, elongation 1.02%.
[0038] The process parameters of the carding process are shown in Table 1:
[0039] Table 1
[0040]
[0041] The process parameters of the drawing process are shown in Table 2:
[0042] Table 2
[0043]
[0044] The main process parameters of the roving process are shown in Table 3: Siro spinning process
[0045] table 3
[0046]
[0047] The...
Embodiment 2
[0052] Design and produce white modal and vegetable dyed fiber 50 / 50 14.8tex blended yarn;
[0053] The spinning process designed and adopted is as follows (indicated by machine model)
[0054] Picking cotton (FA002)→opening (FA106)→ultrasonic cleaning→mixing and opening (FA035)→multi-compartment blending (FA025)→winding (FA076F)→carding (FA226A)→drawing (BHFA1322 together, Two parallels) → roving (FA493) → spun yarn (TH518) → winding (Murata No.21C-s).
[0055] The specific process parameters are as follows:
[0056] Open and clean cotton: with embodiment 1
[0057] Ultrasonic impurity removal: bath ratio 1:30, ultrasonic time 0.5h, frequency 25KHz, hydrochloric acid and 0.1% quaternary ammonium compound surfactant are added to the cleaning solution, and the pH value is 6.3.
[0058] Carding: with embodiment 1
[0059] Drawing: same as embodiment 1
[0060] Roving: with embodiment 1
[0061] Spun yarn: with embodiment 1
[0062] The indigo plant dyed blue fiber was spu...
Embodiment 3
[0065] Design and produce white modal and vegetable dyed fiber 50 / 50 14.8tex blended yarn;
[0066] The spinning process used is as follows (indicated by machine model)
[0067] Cotton picking (FA002)→Cotton opening (FA106)→Ultrasonic impurity removal→Health preservation→Mixed cotton opening (FA035)→Multiple warehouse blending (FA025)→Coiling (FA076F)→Carding (FA226A)→Drawing (BHFA1322- Doubling, double doubling) → roving (FA493) → spun yarn (TH518) → winding (Murata No.21C-s).
[0068] The specific process parameters are as follows:
[0069] Open and clean cotton: with embodiment 1
[0070] Ultrasonic impurity removal: with embodiment 2
[0071] Health:
[0072] Indigo plant dyeing blue fiber: health supplement JF-8059Y-30 amino silicone oil softener owf3%, bath ratio 1:20, spray evenly and treat at 35°C for 12h
[0073] The surface properties of indigo plant-dyed blue fibers before and after the treatment are shown in Table 5:
[0074] table 5
[0075] indigo...
PUM
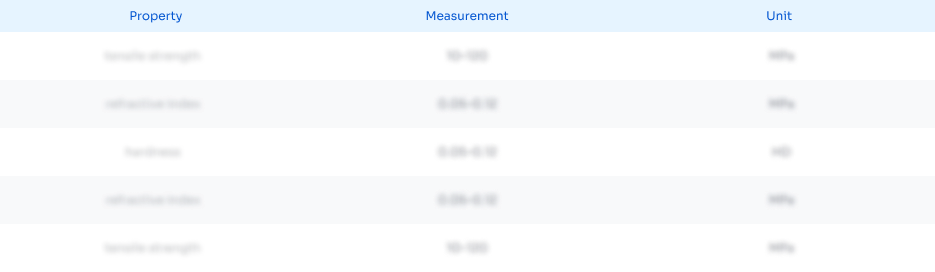
Abstract
Description
Claims
Application Information

- Generate Ideas
- Intellectual Property
- Life Sciences
- Materials
- Tech Scout
- Unparalleled Data Quality
- Higher Quality Content
- 60% Fewer Hallucinations
Browse by: Latest US Patents, China's latest patents, Technical Efficacy Thesaurus, Application Domain, Technology Topic, Popular Technical Reports.
© 2025 PatSnap. All rights reserved.Legal|Privacy policy|Modern Slavery Act Transparency Statement|Sitemap|About US| Contact US: help@patsnap.com