Manufacturing process of mud whistle sound chamber
A technique for producing craft and whistle sounds, which is applied to whistles, musical instruments, sounding instruments, etc. It can solve problems such as time-consuming, complex production process, and slow production speed, and achieve long service life, simple sound chamber production process, and loud sound quality. Effect
- Summary
- Abstract
- Description
- Claims
- Application Information
AI Technical Summary
Problems solved by technology
Method used
Image
Examples
Embodiment
[0019] A manufacturing process of a mud whistle cavity, comprising the following steps:
[0020] S1. Complete the 3D modeling of the mud whistle sound cavity based on 3DMax, in which, the length of the front section of the air hole is 22mm; the length and width of the air hole are both 5mm; the length of the rear section of the air hole is 12mm; the wall thickness of the air hole is 1mm; °;
[0021] S2. Import the model into Maya software, "partition" into layer-by-layer sections, that is, slices, and drive the MakerbotReplicator printer to print layer by layer using PLA 1.75mm 3D lines. The printing sequence: the inner wall of the sound cavity → the sound of the sound cavity → the sound cavity Terminal port→sound cavity whistle→sound cavity outer wall;
[0022] S3. After the printing is completed, use a 3*140mm pointed round file to polish the inner wall, and a 3*140mm flat file to polish the outer wall, and remove the auxiliary support structure and burrs until the sound ca...
PUM
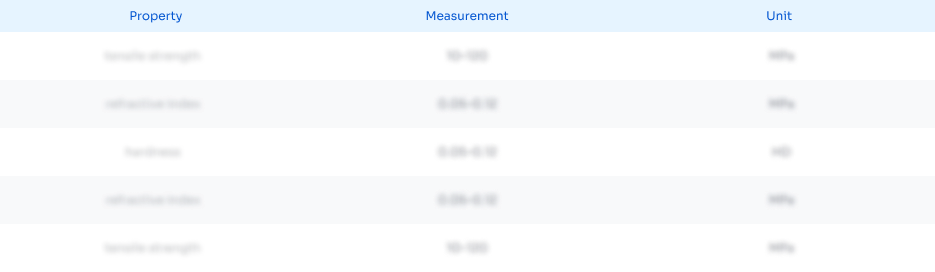
Abstract
Description
Claims
Application Information

- R&D
- Intellectual Property
- Life Sciences
- Materials
- Tech Scout
- Unparalleled Data Quality
- Higher Quality Content
- 60% Fewer Hallucinations
Browse by: Latest US Patents, China's latest patents, Technical Efficacy Thesaurus, Application Domain, Technology Topic, Popular Technical Reports.
© 2025 PatSnap. All rights reserved.Legal|Privacy policy|Modern Slavery Act Transparency Statement|Sitemap|About US| Contact US: help@patsnap.com