Improved bus bar welding machine head
A technology for welding machine heads and bus bars, which is applied to welding power sources, welding power sources, welding equipment, etc., and can solve problems such as difficult full contact, high operation error rate, and increased bus bar welding costs
- Summary
- Abstract
- Description
- Claims
- Application Information
AI Technical Summary
Problems solved by technology
Method used
Image
Examples
specific Embodiment approach 1
[0033] An improved bus bar welding machine head, the main components include: positive electrode overall support plate 1, welding assembly 2, connecting assembly 3, lifting assembly 4, electrode copper plate assembly 5, each welding assembly 2 passes through a connecting assembly 3, a lifting assembly The component 4 can be moved up and down and fixed on the front surface of the positive overall support plate 1; the electrode copper plate component 5 provides welding current for the welding component 2;
[0034] Each lifting assembly 4 includes a cylinder 41 and two groups of sliding structures, each group of sliding structures includes a vertical connecting frame 42, the rear plate surface of the connecting frame 42 is screwed to the positive overall support plate 1, and the front plate surface and the sliding track 43 The screw is fixed, and the slider 44 rigidly fixed on the slider connecting plate 45 is matched and sleeved on the sliding track 43, and the slider connecting ...
specific Embodiment approach 2
[0045] An improved bus bar welding machine head, the main components include: positive electrode overall support plate 1, welding assembly 2, connecting assembly 3, lifting assembly 4, electrode copper plate assembly 5, each welding assembly 2 passes through a connecting assembly 3, a lifting assembly The component 4 can be moved up and down and fixed on the front surface of the positive overall support plate 1; the electrode copper plate component 5 provides welding current for the welding component 2;
[0046] Each lifting assembly 4 includes a cylinder 41 and two groups of sliding structures, each group of sliding structures includes a vertical connecting frame 42, the rear plate surface of the connecting frame 42 is screwed to the positive overall support plate 1, and the front plate surface and the sliding track 43 The screw is fixed, and the slider 44 rigidly fixed on the slider connecting plate 45 is matched and sleeved on the sliding track 43, and the slider connecting ...
PUM
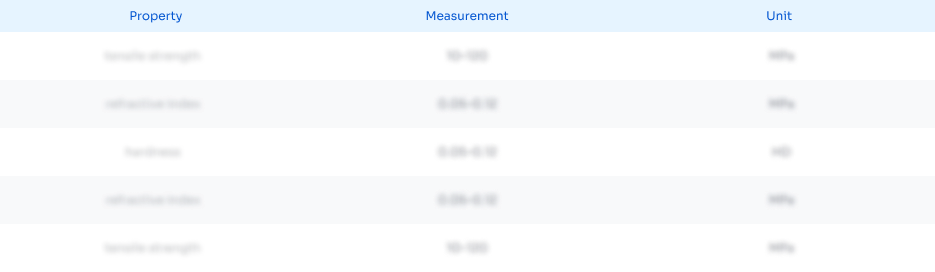
Abstract
Description
Claims
Application Information

- R&D Engineer
- R&D Manager
- IP Professional
- Industry Leading Data Capabilities
- Powerful AI technology
- Patent DNA Extraction
Browse by: Latest US Patents, China's latest patents, Technical Efficacy Thesaurus, Application Domain, Technology Topic, Popular Technical Reports.
© 2024 PatSnap. All rights reserved.Legal|Privacy policy|Modern Slavery Act Transparency Statement|Sitemap|About US| Contact US: help@patsnap.com