A rudder surface clearance wind tunnel test simulation device
A wind tunnel test and simulation device technology, applied in the field of aerospace engineering, can solve problems such as easy mutual interference, easy test accidents, and increase the difficulty of main beam design, and achieve accurate boundary condition simulation, easy modification and control, and systematic effect of small error
- Summary
- Abstract
- Description
- Claims
- Application Information
AI Technical Summary
Problems solved by technology
Method used
Image
Examples
Embodiment Construction
[0031] Such as figure 2 , image 3 , Figure 4 As shown, the present invention includes: 1 model, 2 model fixed flange, 3 model main shaft, 4 model fixed sleeve, 5 bearing, 6 torsion spring plate, 7 emergency limit nail, 8 model protection column, 9 gap control screw / Bolt, 10 fixed base
[0032] One end of the model fixing flange 2 is fixedly connected to the model 1, and the other end is fixedly connected to the model main shaft 3. The middle section of the main shaft 3 of the model is a circular section, and the two ends are rectangular sections. The rectangular section beam connected to the torsion spring plate is used for fixing, and the rectangular section beam connected to the flange is used to simulate the bending stiffness of the model. Through the torsion spring plate 6 The bending realizes the control of the torsional stiffness of the model. Bearing 5 is installed in model fixed cover 4 inside, and model main shaft 3 passes two bearings 5. The inner diameter o...
PUM
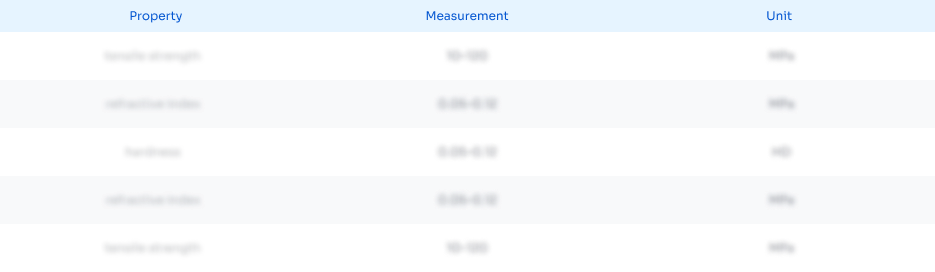
Abstract
Description
Claims
Application Information

- Generate Ideas
- Intellectual Property
- Life Sciences
- Materials
- Tech Scout
- Unparalleled Data Quality
- Higher Quality Content
- 60% Fewer Hallucinations
Browse by: Latest US Patents, China's latest patents, Technical Efficacy Thesaurus, Application Domain, Technology Topic, Popular Technical Reports.
© 2025 PatSnap. All rights reserved.Legal|Privacy policy|Modern Slavery Act Transparency Statement|Sitemap|About US| Contact US: help@patsnap.com