Installation method of spliced floor
An installation method and floor technology, which are applied to the joining of wooden veneers, adhesive application devices, wood processing appliances, etc., can solve the problems of low processing efficiency, large labor consumption, lack of systematization, etc., and achieve convenient operation and simple structure. Effect
- Summary
- Abstract
- Description
- Claims
- Application Information
AI Technical Summary
Problems solved by technology
Method used
Image
Examples
Embodiment Construction
[0016] Combine below Figure 1-4 The present invention is described in detail, and for convenience of description, the orientations mentioned below are now stipulated as follows: figure 1 The up, down, left, right, front and back directions of the projection relationship itself are the same.
[0017] refer to Figure 1-4 , according to an embodiment of the present invention, a splicing floor installation method includes a device main body 10, a gluing device arranged in the device main body 10, and an extrusion device arranged in the device main body 10, the gluing device The glue device includes a first working chamber 11 arranged in the device main body 10, a motor 12 is fixed in the upper end wall of the first working chamber 11, and a motor 12 extending downward is fixed on the output shaft of the motor 12. The screw rod 13 is fixed on the screw rod 13 with an inner ratchet 14, the rear end of the inner ratchet 14 is meshed and connected with a first bevel gear 15, and t...
PUM
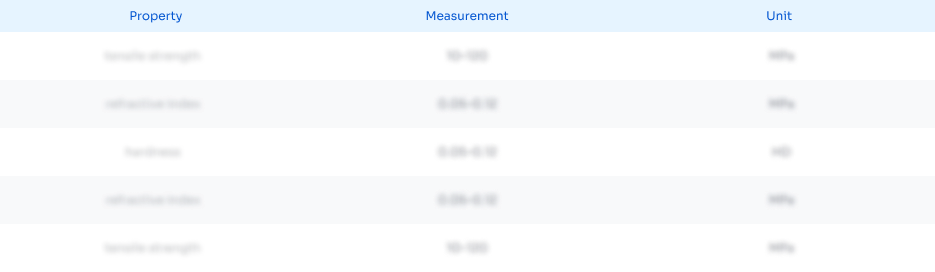
Abstract
Description
Claims
Application Information

- R&D Engineer
- R&D Manager
- IP Professional
- Industry Leading Data Capabilities
- Powerful AI technology
- Patent DNA Extraction
Browse by: Latest US Patents, China's latest patents, Technical Efficacy Thesaurus, Application Domain, Technology Topic, Popular Technical Reports.
© 2024 PatSnap. All rights reserved.Legal|Privacy policy|Modern Slavery Act Transparency Statement|Sitemap|About US| Contact US: help@patsnap.com