Four-joint plane robot
A four-joint, robot technology, used in manipulators, program-controlled manipulators, manufacturing tools, etc., can solve the problems of reducing the rigidity and accuracy of the robot, the excessive moment of inertia of the robot, and the limited rotation range of the robot, so as to improve the rigidity and operation of the robot. Easy maintenance and compact structure
- Summary
- Abstract
- Description
- Claims
- Application Information
AI Technical Summary
Problems solved by technology
Method used
Image
Examples
Embodiment Construction
[0024] In order to make the technical means, creative features, goals and effects achieved by the present invention easy to understand, the present invention will be further elaborated below.
[0025] Such as Figure 1 to Figure 4 As shown, a four-joint planar robot includes a first joint part 1, a second joint part 2 installed in the first joint part 1 for linear motion up and down, and a third joint part 3 installed on the upper end of the second joint part 2 . The fourth joint part 4 installed at the lower end of the third joint part 3, the first joint part 1 includes a base 11, the front end of the base 11 is provided with a ball screw 12, and the rear end is provided with symmetrically arranged auxiliary fixing columns 13. A plastic drag chain 14 is provided on the outer wall of the base 11, one end of the plastic drag chain 14 is fixed to the base 11 and the other end is fixed to the second joint part 2;
[0026] The second joint part 2 includes a lifting base 21, a hol...
PUM
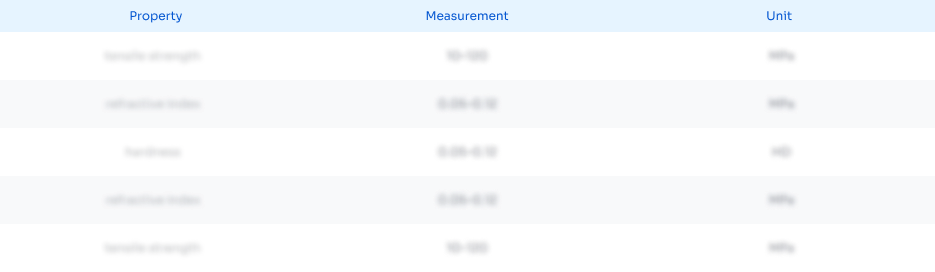
Abstract
Description
Claims
Application Information

- R&D Engineer
- R&D Manager
- IP Professional
- Industry Leading Data Capabilities
- Powerful AI technology
- Patent DNA Extraction
Browse by: Latest US Patents, China's latest patents, Technical Efficacy Thesaurus, Application Domain, Technology Topic, Popular Technical Reports.
© 2024 PatSnap. All rights reserved.Legal|Privacy policy|Modern Slavery Act Transparency Statement|Sitemap|About US| Contact US: help@patsnap.com