Elastically-driven modular joint with force feedback control
A modular joint and elastic drive technology, applied in the field of robotics, can solve the problems of high rigidity, lack of environmental adaptability and interactivity of robots, and achieve the effects of increasing flexibility and compactness, facilitating wiring, and expanding the range of motion
- Summary
- Abstract
- Description
- Claims
- Application Information
AI Technical Summary
Problems solved by technology
Method used
Image
Examples
Embodiment Construction
[0013] The present invention will be further described below in conjunction with the accompanying drawings, and the purpose and effect of the present invention will become more obvious.
[0014] The elastic drive modular joint with force feedback control of the present invention includes two parts: a joint transmission device and a force signal detection device, specifically, it includes: a motor casing 1, a first end cover 2, an encoder 3, a first bearing 4, a Er sensor 5, motor rotor 6, motor stator 7, motor flange 8, harmonic reducer 9, hollow cable shaft 13, output shaft 15, cross roller bearing 16, first absolute angle sensor 18, joint housing 22 , Elastic torsion spring 25, bearing 26, joint flange 27, output end cover 28, second end cover 29, second bearing 30 and second absolute angle sensor 31, etc.
[0015] The motor stator 7 is installed in the motor casing 1, and its axial position is determined by the first end cover 2 and the motor flange 8. The motor stator 7, t...
PUM
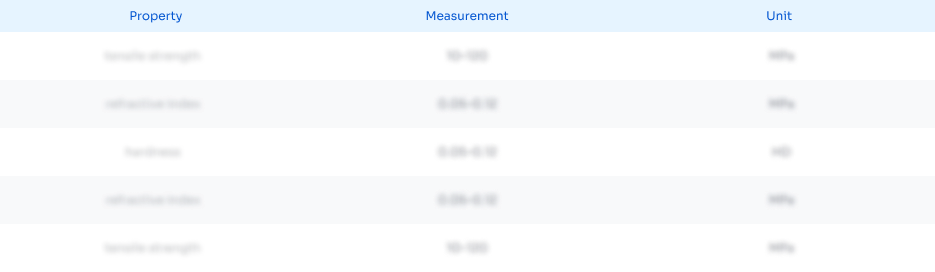
Abstract
Description
Claims
Application Information

- R&D
- Intellectual Property
- Life Sciences
- Materials
- Tech Scout
- Unparalleled Data Quality
- Higher Quality Content
- 60% Fewer Hallucinations
Browse by: Latest US Patents, China's latest patents, Technical Efficacy Thesaurus, Application Domain, Technology Topic, Popular Technical Reports.
© 2025 PatSnap. All rights reserved.Legal|Privacy policy|Modern Slavery Act Transparency Statement|Sitemap|About US| Contact US: help@patsnap.com