Two-side printing two-time water-washing dyeing and finishing process
A double-sided printing, dyeing and finishing technology, applied in the field of dyeing and finishing technology, can solve the problems of fabrics such as general hydrophilicity and softness, no individuality, etc., and achieve the effect of strong color fixing performance and reasonable design
- Summary
- Abstract
- Description
- Claims
- Application Information
AI Technical Summary
Problems solved by technology
Method used
Examples
Embodiment Construction
[0015] All the features disclosed in this specification, or all disclosed methods or steps in the process, except for mutually exclusive features and / or steps, can be combined in any manner.
[0016] Any feature in this specification, unless specifically stated, can be replaced by other equivalent or equivalent alternative features. That is, unless otherwise stated, each feature is just one example of a series of equivalent or similar features.
[0017] A dyeing and finishing process for knitted fabrics during use, which includes the following steps:
[0018] Step one, prepare the original cloth: prepare the original cloth, check the quality of the original cloth, turn the cloth and sew;
[0019] Step two, processing the original fabric: singe on the prepared fabric to make the fabric smooth;
[0020] Step three, one water washing: Put the fabric into water at 30-50 degrees Celsius for washing, and stir during the washing process.
[0021] Step 4: Dyeing: dye the desizing fabric;
[0022...
PUM
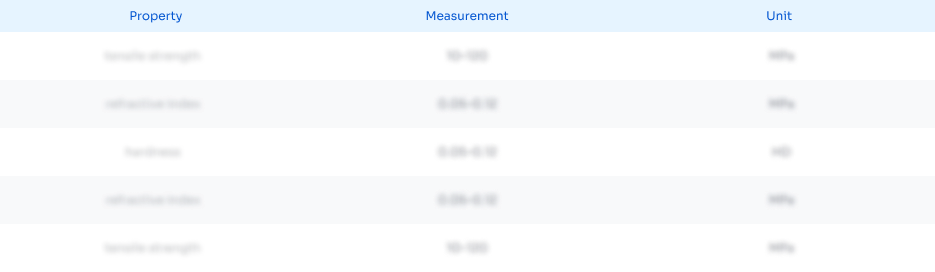
Abstract
Description
Claims
Application Information

- Generate Ideas
- Intellectual Property
- Life Sciences
- Materials
- Tech Scout
- Unparalleled Data Quality
- Higher Quality Content
- 60% Fewer Hallucinations
Browse by: Latest US Patents, China's latest patents, Technical Efficacy Thesaurus, Application Domain, Technology Topic, Popular Technical Reports.
© 2025 PatSnap. All rights reserved.Legal|Privacy policy|Modern Slavery Act Transparency Statement|Sitemap|About US| Contact US: help@patsnap.com