Thermal displacement compensation apparatus
A technology of thermal displacement and workpiece, applied in the direction of biological neural network model, measurement/indicating equipment, program control, etc., can solve the problems of hindering shape inspection and unrealistic, and achieve the effect of high-precision measurement error
- Summary
- Abstract
- Description
- Claims
- Application Information
AI Technical Summary
Problems solved by technology
Method used
Image
Examples
Embodiment Construction
[0026] Figure 1A It is a schematic hardware configuration diagram showing main parts of the thermal displacement correction device of the first embodiment.
[0027] The CPU 11 included in the thermal displacement correction device 1 of the present embodiment is a processor that controls the thermal displacement correction device 1 as a whole. The CPU 11 reads the system program stored in the ROM 12 via the bus 20, and controls the entire thermal displacement correction device 1 according to the system program. Temporary calculation data, display data, and various data input from a control device and a shape measuring device described later are temporarily stored in the RAM 13 .
[0028] The nonvolatile memory 14 is configured, for example, as a memory that is backed up by an unillustrated battery or the like and maintains a storage state even if the power supply of the thermal displacement correction device 1 is cut off, and stores various programs and programs input through ...
PUM
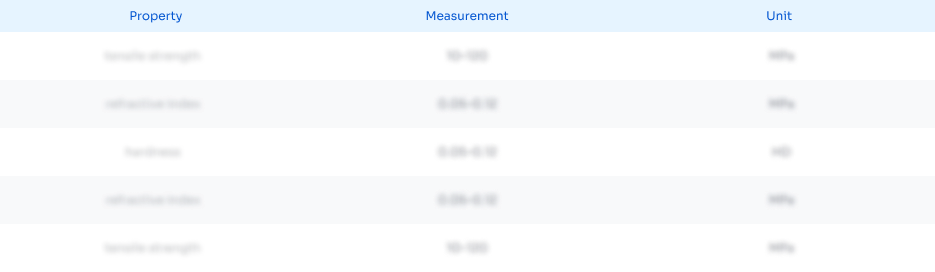
Abstract
Description
Claims
Application Information

- R&D Engineer
- R&D Manager
- IP Professional
- Industry Leading Data Capabilities
- Powerful AI technology
- Patent DNA Extraction
Browse by: Latest US Patents, China's latest patents, Technical Efficacy Thesaurus, Application Domain, Technology Topic, Popular Technical Reports.
© 2024 PatSnap. All rights reserved.Legal|Privacy policy|Modern Slavery Act Transparency Statement|Sitemap|About US| Contact US: help@patsnap.com