Disassembling method for double-tightness chuck
A chuck and tightness technology, which is applied to the supporting elements of the blade, preventing leakage, and engine components, can solve the problem that the double-tightness chuck cannot be decomposed, and achieves the effect of eliminating friction and interference and stabilizing the decomposition process.
- Summary
- Abstract
- Description
- Claims
- Application Information
AI Technical Summary
Problems solved by technology
Method used
Image
Examples
Embodiment Construction
[0051] Below in conjunction with accompanying drawing, the present invention is described in detail.
[0052] Such as figure 1 , figure 2 As shown, a disassembly device for a double-tightness chuck provided by the present invention includes a lifting mechanism 1, a body 2, a rotating mechanism 3, an outer ring lifting mechanism 4, a backing plate 5, a gripping mechanism 6 and an auxiliary gripping mechanism 7, wherein , the backing plate 5 is placed under the outer ring lifting mechanism 4, and the turbine disk to be separated is placed in the cavity between the backing plate 5 and the outer ring lifting mechanism 4; the grasping mechanism 6 and the auxiliary grasping mechanism 7 are installed outside In the central hole of the ring lifting mechanism 4, the body 2 is installed on the upper surface of the outer ring lifting mechanism 4, and the body 2 is also connected with the lifting mechanism 1.
[0053] specifically:
[0054] Such as image 3 As shown, the lifting mech...
PUM
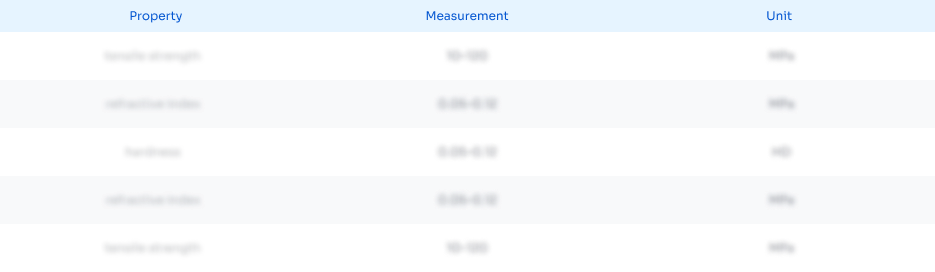
Abstract
Description
Claims
Application Information

- R&D Engineer
- R&D Manager
- IP Professional
- Industry Leading Data Capabilities
- Powerful AI technology
- Patent DNA Extraction
Browse by: Latest US Patents, China's latest patents, Technical Efficacy Thesaurus, Application Domain, Technology Topic, Popular Technical Reports.
© 2024 PatSnap. All rights reserved.Legal|Privacy policy|Modern Slavery Act Transparency Statement|Sitemap|About US| Contact US: help@patsnap.com