Serial robot kinematic calibration method and system
A robot kinematics and calibration method technology, which is applied in the field of six-degree-of-freedom serial industrial robot kinematics calibration, can solve the problems of difficulty, the influence of the deployment environment of the robot base on the calibration result, and the non-universal calibration tooling, etc., to improve absolute positioning The effect of precision
- Summary
- Abstract
- Description
- Claims
- Application Information
AI Technical Summary
Problems solved by technology
Method used
Image
Examples
Embodiment Construction
[0022] In order to make the technical solutions and advantages in the embodiments of the present application clearer, the exemplary embodiments of the present application will be further described in detail below in conjunction with the accompanying drawings. Apparently, the described embodiments are only part of the embodiments of the present application, and Not an exhaustive list of all embodiments. It should be noted that, in the case of no conflict, the embodiments in the present application and the features in the embodiments can be combined with each other.
[0023] The core idea of this scheme is to use the universal calibration tooling and laser tracker to accurately measure the end position of the robot, complete the accurate parameter identification of the kinematics of the six-degree-of-freedom serial industrial robot, and realize the motion compensation algorithm in the control of the industrial robot, effectively improving the industrial The absolute precision ...
PUM
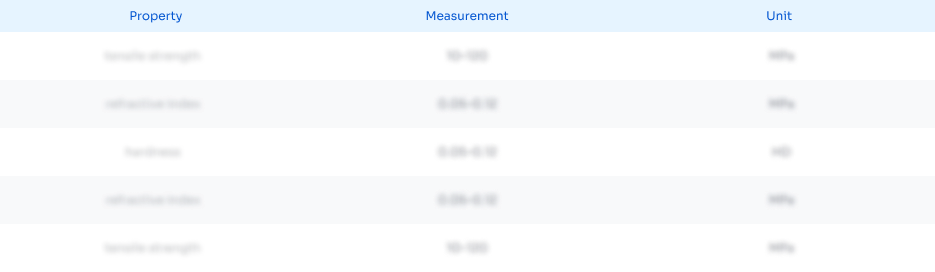
Abstract
Description
Claims
Application Information

- R&D
- Intellectual Property
- Life Sciences
- Materials
- Tech Scout
- Unparalleled Data Quality
- Higher Quality Content
- 60% Fewer Hallucinations
Browse by: Latest US Patents, China's latest patents, Technical Efficacy Thesaurus, Application Domain, Technology Topic, Popular Technical Reports.
© 2025 PatSnap. All rights reserved.Legal|Privacy policy|Modern Slavery Act Transparency Statement|Sitemap|About US| Contact US: help@patsnap.com