Internal heat generating material coupled hydrocarbon cracking
A technology for exothermic materials and pyrolysis products, which is applied in the field of pyrolysis of hydrocarbon feeds in combination with exothermic materials and hydrocarbon cracking processes, and can solve problems such as energy consumption
- Summary
- Abstract
- Description
- Claims
- Application Information
AI Technical Summary
Problems solved by technology
Method used
Image
Examples
example
[0040] The following examples are illustrative of embodiments of the invention and are not intended to limit the scope of the disclosed embodiments.
[0041]Experimental data were obtained to demonstrate the effect of hydrocarbon cracking reactions in combination with HGM. The catalytic reaction is carried out in a fixed bed flow reactor operated at atmospheric pressure. The reactor was charged with catalyst having a mass of 9 to 12 g, which was trayed and sieved to a diameter of 425-800 micrometers (μm). The catalyst was a ZSM-5 microporous molecular sieve purchased from Nankai University Catalyst Co. Before the catalytic reaction, the catalyst contains N 2 (120cm 3 min -1 ) to the desired reaction temperature and held overnight. The fixed bed flow reactor was heated to the desired reaction temperature using a 3-zone electric heater. At the desired reaction temperature (typically between 250-850°C), the reactants, which are selected from n-hexane, naphtha and formaldeh...
PUM
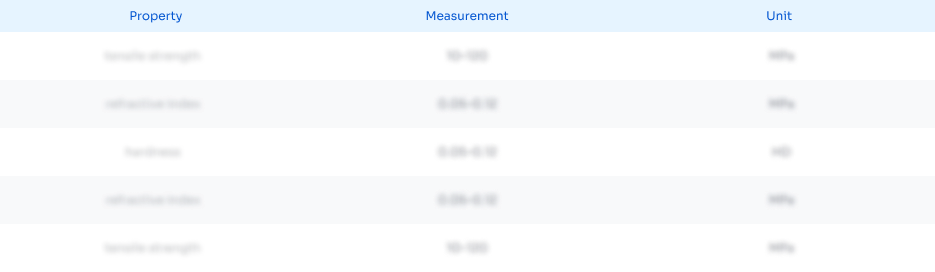
Abstract
Description
Claims
Application Information

- R&D
- Intellectual Property
- Life Sciences
- Materials
- Tech Scout
- Unparalleled Data Quality
- Higher Quality Content
- 60% Fewer Hallucinations
Browse by: Latest US Patents, China's latest patents, Technical Efficacy Thesaurus, Application Domain, Technology Topic, Popular Technical Reports.
© 2025 PatSnap. All rights reserved.Legal|Privacy policy|Modern Slavery Act Transparency Statement|Sitemap|About US| Contact US: help@patsnap.com