Welding and correcting dual-purpose base
A dual-purpose, sliding seat technology, used in welding equipment, welding equipment, auxiliary welding equipment, etc., can solve the problems of unsuitable batch calibration, troublesome transfer, low degree of automation, etc., to shorten the production cycle and facilitate the application of welding torches. Welding, high degree of automation effect
- Summary
- Abstract
- Description
- Claims
- Application Information
AI Technical Summary
Problems solved by technology
Method used
Image
Examples
Embodiment 1
[0035] Embodiment one: if Figure 6 , Figure 7 and Figure 8 As shown, it is mainly aimed at the welding and correction of U-shaped steel structure 21. The working process is as follows: the initial state is as follows Figure 6 As shown, the lower positioning correction wheel 6 is placed in the U-shaped seat 3, and the lower positioning correction wheel 6 is flush with the supporting surface 2a. After the plate of the U-shaped steel structure 21 is initially spot-welded, it is erected on a multi-row base arranged in parallel. On the beam 1, place the main part of the U-shaped steel structure on the outer corner frame 2 and the lower positioning correction wheel 6, and place the side part of the U-shaped steel structure 21 on the retaining surface 7c, and then insert the welding torch into the U-shaped steel The joints of the corners of the structure 21 are welded, using an automatic welding machine to move along the length direction of the U-shaped steel structure 21 to co...
Embodiment 2
[0036] Embodiment two: if Figure 9 , Figure 10 and Figure 11 As shown, it is mainly aimed at the I-shaped steel structure 22, and the working process is as follows: the plate of the I-shaped steel structure 22 to be welded is initially spot-welded, and then the main part of the I-shaped steel structure 22 is placed on the supporting surface 2a , and make the side of the I-shaped steel structure 22 against the retaining surface 7c, then the welding torch can be inserted into the corner of the inner side of the I-shaped steel structure 22 for welding, and the automatic welding machine can be used to weld along the side of the I-shaped steel structure 22. The movement of the length direction of the steel structure 22, thereby completing the overall welding process to the I-shaped steel structure 22; after the welding is completed, the welding torch is withdrawn, and the lower drive cylinder 4 is started, so that the push-down shaft 5 drives the lower positioning correction wh...
PUM
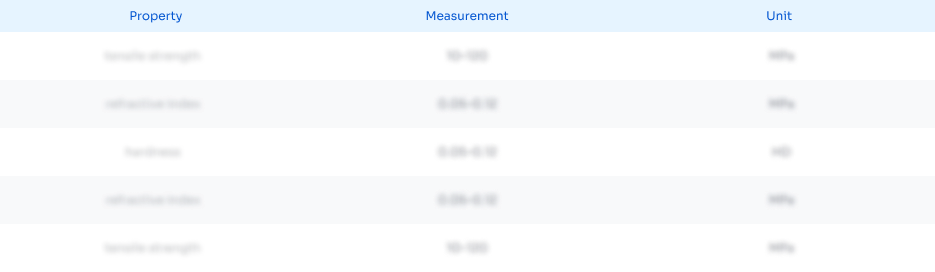
Abstract
Description
Claims
Application Information

- R&D Engineer
- R&D Manager
- IP Professional
- Industry Leading Data Capabilities
- Powerful AI technology
- Patent DNA Extraction
Browse by: Latest US Patents, China's latest patents, Technical Efficacy Thesaurus, Application Domain, Technology Topic, Popular Technical Reports.
© 2024 PatSnap. All rights reserved.Legal|Privacy policy|Modern Slavery Act Transparency Statement|Sitemap|About US| Contact US: help@patsnap.com