A lightweight forward design method and system for automobile structure based on multiple performance constraints
A technology of automobile structure and design method, which is applied in the field of automobile CAE simulation, can solve the problems of lack of systematic and overall design methods, and achieve the effect of improving design efficiency, shortening design cycle, and improving the level of forward development
- Summary
- Abstract
- Description
- Claims
- Application Information
AI Technical Summary
Problems solved by technology
Method used
Image
Examples
Embodiment Construction
[0041] The flow process that the inventive method realizes is as figure 1 Shown:
[0042] Step 1: Build a CAE simulation analysis model
[0043] Build the finite element analysis model of the body structure, and carry out the simulation analysis of the body performance.
[0044] Step 2: Topology Optimization
[0045] Using topology optimization technology, taking the bending / torsional stiffness performance of the car body as the constrained working condition, the material distribution in the design area is obtained, and the typical force transmission path of the automobile structure is identified;
[0046] Step 3: Sensitivity Analysis
[0047] Use sensitivity analysis technology to carry out strain energy analysis and material thickness sensitivity analysis respectively to find the weak link and critical design area of the car body;
[0048] Step 4: Shape Ribbing / Size Optimization
[0049] Perform morphology optimization, determine the optimal structural morphology sche...
PUM
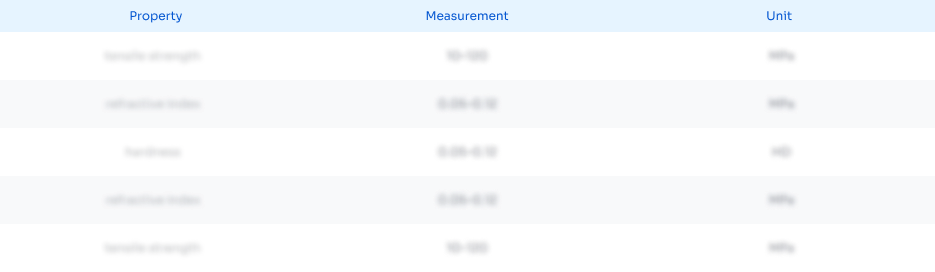
Abstract
Description
Claims
Application Information

- R&D
- Intellectual Property
- Life Sciences
- Materials
- Tech Scout
- Unparalleled Data Quality
- Higher Quality Content
- 60% Fewer Hallucinations
Browse by: Latest US Patents, China's latest patents, Technical Efficacy Thesaurus, Application Domain, Technology Topic, Popular Technical Reports.
© 2025 PatSnap. All rights reserved.Legal|Privacy policy|Modern Slavery Act Transparency Statement|Sitemap|About US| Contact US: help@patsnap.com