A Method for Measuring the Vertical Section Deformation of Shipborne Large Radar Base
A measurement method and technology of the vertical section, which is applied in the field of deformation measurement of the vertical section of the shipboard large-scale radar base, can solve the problems that the equipment system occupies a large deck space, and the dedicated optical channel is difficult to guarantee, so as to improve the radar measurement accuracy and occupy a small space , The effect of convenient operation and implementation
- Summary
- Abstract
- Description
- Claims
- Application Information
AI Technical Summary
Problems solved by technology
Method used
Image
Examples
Embodiment Construction
[0049]The specific implementation manners of the present invention will be further described below in conjunction with the drawings and examples. The following examples are only used to illustrate the technical solution of the present invention more clearly, but not to limit the protection scope of the present invention.
[0050] The invention relates to a method for measuring the deformation of the vertical section of a ship-borne large-scale radar base. The measurement method is to install the optical fiber Bragg grating sensor on the radar in sections along the port side, starboard side, bow side and stern side of the ship. For the inner wall of the barrel wall of the base, determine the deformation measurement and calculation method according to the installation plan, including the following measurement steps:
[0051] Step 1. Determine the installation position of the sensor: the optical fiber sensor used for deformation measurement should be installed in sections along t...
PUM
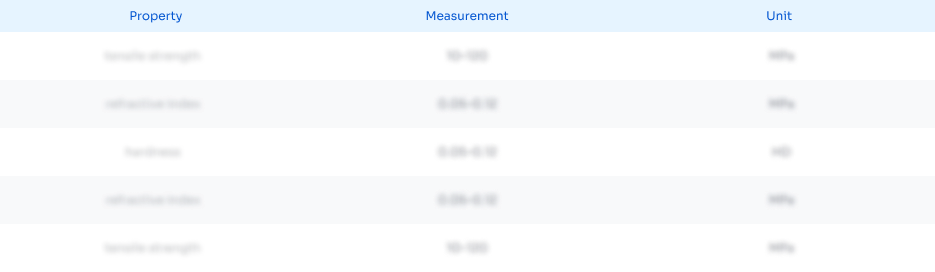
Abstract
Description
Claims
Application Information

- R&D
- Intellectual Property
- Life Sciences
- Materials
- Tech Scout
- Unparalleled Data Quality
- Higher Quality Content
- 60% Fewer Hallucinations
Browse by: Latest US Patents, China's latest patents, Technical Efficacy Thesaurus, Application Domain, Technology Topic, Popular Technical Reports.
© 2025 PatSnap. All rights reserved.Legal|Privacy policy|Modern Slavery Act Transparency Statement|Sitemap|About US| Contact US: help@patsnap.com