Profile steel concrete transfer beam and reverse construction method thereof
A construction method and transfer beam technology, which is applied in the direction of joists, girders, truss beams, etc., can solve the problems of large cracks in steel concrete transfer beams and low utilization rate of steel materials, so as to increase the utilization rate of materials, reduce loads, and reduce Effect of number of cracks and crack width
- Summary
- Abstract
- Description
- Claims
- Application Information
AI Technical Summary
Problems solved by technology
Method used
Image
Examples
Embodiment 1
[0043] Step i. Construction of Substructure Column 1.
[0044] Step ii. Construct the profiled steel 2 in the steel-concrete transfer beam.
[0045] Step iii. Construct part or all of the superstructure 3 .
[0046] Step ⅳ. Construct the steel bar 4 of the steel-concrete transfer beam, and pour concrete 5 .
[0047] Step v. If there is a remaining part of the superstructure 3, construct the remaining part.
Embodiment 2
[0049] Step i. Construction of Substructure Column 1.
[0050] Step ⅱ. Construct the profiled steel 2 in the steel-concrete transfer beam, and bind the steel bars 3.
[0051] Step iii. Construct part or all of the superstructure 3 .
[0052] Step ⅳ. Concrete 5 for the construction of steel-concrete transfer beams.
[0053] Step v. If there is a remaining part of the superstructure 3, construct the remaining part.
Embodiment 3
[0055] Step i. Construction of Substructure Column 1.
[0056] Step ⅱ. Construct the profiled steel 2 in the steel-concrete transfer beam.
[0057] Step Ⅲ. Construct part or all of the superstructure 3, and bind the steel bars 4 in the steel-concrete transfer beam.
[0058] Step ⅳ. Concrete 5 for the construction of steel-concrete transfer beams.
[0059] Step v. If there is a remaining part of the superstructure 3, construct the remaining part.
[0060] Calculation is required before reverse construction to determine the construction scope of the steel section and superstructure 3, so that the steel section 2 can bear the load of the superstructure 3, and the live load of the actual situation should also be considered during design calculation and implementation.
[0061] The invention can reduce the load borne by the reinforced concrete part in the transfer beam, effectively reduce the number and width of cracks in the transfer beam to steel concrete, and simultaneously in...
PUM
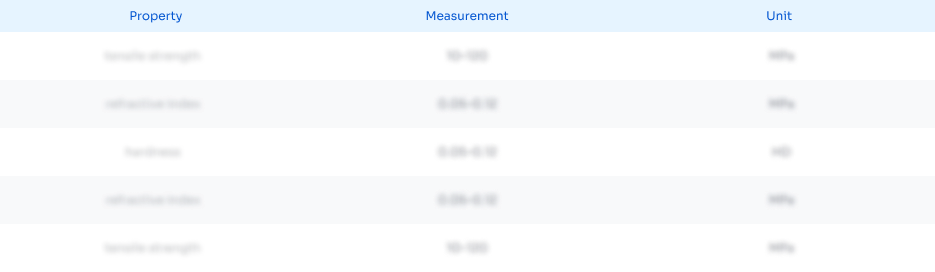
Abstract
Description
Claims
Application Information

- R&D
- Intellectual Property
- Life Sciences
- Materials
- Tech Scout
- Unparalleled Data Quality
- Higher Quality Content
- 60% Fewer Hallucinations
Browse by: Latest US Patents, China's latest patents, Technical Efficacy Thesaurus, Application Domain, Technology Topic, Popular Technical Reports.
© 2025 PatSnap. All rights reserved.Legal|Privacy policy|Modern Slavery Act Transparency Statement|Sitemap|About US| Contact US: help@patsnap.com