Modified ABS material, preparation method and application
An ABS material and modified technology, applied in the direction of metal processing, etc., can solve the problems of inconvenient adjustment of the rotation direction of the drill bit, disassembly and assembly, hole punching, and strong drilling limitations, so as to improve drilling efficiency and stability, prevent The effect of bias
- Summary
- Abstract
- Description
- Claims
- Application Information
AI Technical Summary
Problems solved by technology
Method used
Image
Examples
Embodiment Construction
[0014] Combine below Figure 1-4 The present invention will be described in detail.
[0015] refer to Figure 1-4 , a modified ABS material and its preparation method and application according to an embodiment of the present invention, comprising a substrate 100, the top end surface of the substrate 100 is symmetrically fixed with a vertical frame 101, and the vertical frames 101 on the left and right sides are fixed An outer frame 107 is provided, and a first sliding space 113 is provided in the bottom end surface of the outer frame 107, and an embedding seat 108 is installed in the first sliding space 113, and the top surface of the embedding seat 108 is in contact with the The top wall of the first sliding space 113 is press-fitted with a buffer elastic piece 112, and the bottom end surface of the mounting seat 108 is provided with a first notch 145, and the mounting seat on the upper side of the first notch 145 108 is provided with a first conduction cavity 132, and the ...
PUM
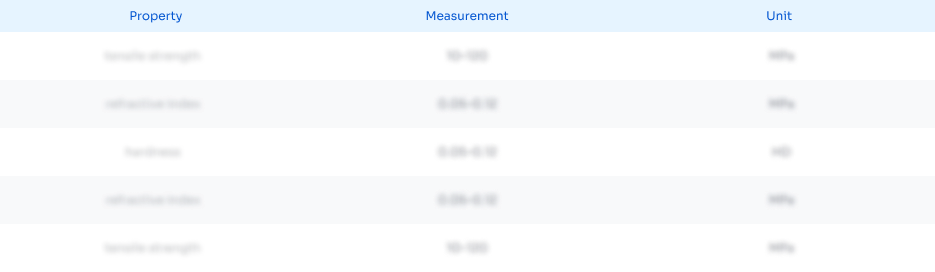
Abstract
Description
Claims
Application Information

- Generate Ideas
- Intellectual Property
- Life Sciences
- Materials
- Tech Scout
- Unparalleled Data Quality
- Higher Quality Content
- 60% Fewer Hallucinations
Browse by: Latest US Patents, China's latest patents, Technical Efficacy Thesaurus, Application Domain, Technology Topic, Popular Technical Reports.
© 2025 PatSnap. All rights reserved.Legal|Privacy policy|Modern Slavery Act Transparency Statement|Sitemap|About US| Contact US: help@patsnap.com