A kind of preparation method of negative electrode material of lithium ion battery
A lithium-ion battery and negative electrode material technology, applied in battery electrodes, secondary batteries, circuits, etc., can solve the problems of electrode material crushing, poor cycle stability, etc., and achieve the effect of enhanced conductivity, enhanced conductivity, and simple experimental schemes
- Summary
- Abstract
- Description
- Claims
- Application Information
AI Technical Summary
Problems solved by technology
Method used
Image
Examples
Embodiment 1
[0032] The first step, preparation of CuS material
[0033] 1. Dissolve 0.01mol of copper chloride dihydrate (1.70g) into 35ml of ethylene glycol, and stir until completely dissolved to form a green solution (A);
[0034] 2. Take another beaker, dissolve 0.04mol thiourea (3.04g) into 35ml ethylene glycol, and stir until completely dissolved to obtain solution (B);
[0035] 3. Add all the thiourea solution (B) into the copper chloride solution (A), and stir while heating (heating temperature 60°C). After stirring for 5 minutes, white flocculent precipitates will appear in the solution, and it will become milky after stirring for 10 minutes. solution, after 10min the solution turned into a yellow mixture;
[0036] 4. Transfer the solution into the high-pressure hydrothermal reactor and close the reactor;
[0037] 5. Put the reaction kettle in a constant temperature oven, raise the temperature to 140°C, then store it at a constant temperature at 140°C for 4 hours, and then cool...
Embodiment 2
[0048] 1. Dissolve 0.02mol of copper chloride dihydrate (3.40g) into 70ml of ethylene glycol, stir until completely dissolved, and generate a green solution (A);
[0049] 2. Take another beaker, dissolve 0.08mol thiourea (6.08g) into 70ml ethylene glycol, and stir it until it is completely dissolved to obtain solution (B);
[0050] 3. Add all the thiourea solution (B) into the copper chloride solution (A), and stir while heating (heating temperature 70°C). After stirring for 6 minutes, white flocculent precipitates will appear in the solution, and it will become milky after stirring for 10 minutes. solution, after 10min the solution turned into a yellow mixture;
[0051] 4. Transfer the solution into the high-pressure hydrothermal reactor and close the reactor;
[0052] 5. Place the reaction kettle in a constant temperature oven, raise the temperature to 150°C, then store it at a constant temperature at 150°C for 3 hours, and then cool it down to room temperature naturally; ...
Embodiment 3
[0066] 1. Dissolve 0.03mol of copper chloride dihydrate (5.10g) into 105ml of ethylene glycol, stir until completely dissolved, and generate a green solution (A);
[0067] 2. Take another beaker, dissolve 0.12mol thiourea (9.12g) into 105ml ethylene glycol, and stir it until it is completely dissolved to obtain solution (B);
[0068] 3. Add all the thiourea solution (B) into the copper chloride solution (A), and stir while heating (heating temperature 80°C). After stirring for 7 minutes, white flocculent precipitates will appear in the solution, and it will become milky after stirring for 10 minutes. solution, after 10min the solution turned into a yellow mixture;
[0069] 4. Transfer the solution into the high-pressure hydrothermal reactor and close the reactor;
[0070] 5. Place the reaction kettle in a constant temperature oven, raise the temperature to 160°C, then store it at a constant temperature at 160°C for 2 hours, and then cool it down to room temperature naturally;...
PUM
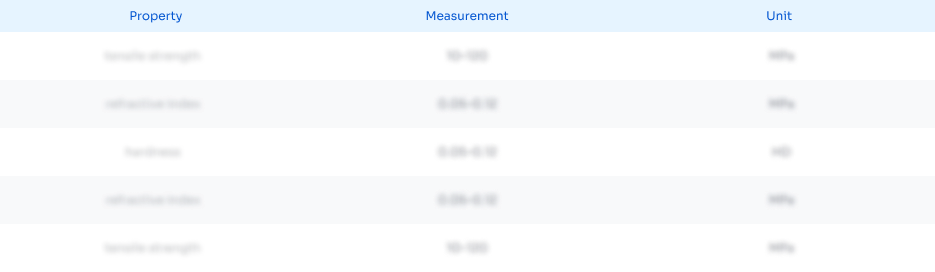
Abstract
Description
Claims
Application Information

- R&D Engineer
- R&D Manager
- IP Professional
- Industry Leading Data Capabilities
- Powerful AI technology
- Patent DNA Extraction
Browse by: Latest US Patents, China's latest patents, Technical Efficacy Thesaurus, Application Domain, Technology Topic, Popular Technical Reports.
© 2024 PatSnap. All rights reserved.Legal|Privacy policy|Modern Slavery Act Transparency Statement|Sitemap|About US| Contact US: help@patsnap.com