Polypropylene fiber continuous glass fiber blended thermal composite reinforcing material and preparation method thereof
A polypropylene fiber, glass fiber technology, applied in fiber processing, fiber types, textiles and papermaking, etc., can solve the problems of low production efficiency, complex preparation process, unsatisfactory bonding performance, etc., to achieve high production efficiency, simple equipment, The effect of easy-to-master technology
- Summary
- Abstract
- Description
- Claims
- Application Information
AI Technical Summary
Problems solved by technology
Method used
Examples
Embodiment 1
[0022] (1) Preparation of polypropylene fiber: take drawing-grade polypropylene brand-new pellets as ingredients, add appropriate compatibilizer to polypropylene, and add compound antioxidant to the ingredients, and the compound antioxidant is determined by mass fraction 28% of antioxidant 1010, 12% of antioxidant 1024, 23% of Omnistab 46, and 15% of antioxidant 2246 were used to obtain polypropylene fibers, and the oxidation induction time of polypropylene fibers was greater than 30 minutes.
[0023] (2) Surface carboxylation of polypropylene fibers: The monofilament of polypropylene (PP) fibers is drawn through a three-roller winder through a certain temperature of K 2 Cr 2 o 7 and sulfuric acid mixed solution, the time of PP fiber monofilament in the mixed solution is about 1 minute, and the K in the mixed solution 2 Cr 2 o 7 The concentration is 0.1mol / L, the concentration of sulfuric acid is 2mol / L, and the treatment temperature is 50°C. After washing with alkaline wa...
Embodiment 2
[0028] (1) Preparation of polypropylene fiber: take drawing-grade polypropylene brand-new pellets as ingredients, add appropriate compatibilizer to polypropylene, and add compound antioxidant to the ingredients, and the compound antioxidant is determined by mass fraction 28% of antioxidant 1010, 12% of antioxidant 1024, 23% of Omnistab 46, and 15% of antioxidant 2246 were used to obtain polypropylene fibers, and the oxidation induction time of polypropylene fibers was greater than 30 minutes.
[0029] (2) Surface carboxylation of polypropylene fiber: The PP fiber monofilament drawn by a three-roller winder is continuously passed through a certain temperature of K 2 Cr 2 o 7 and sulfuric acid mixed solution, the time of PP fiber monofilament in the mixed solution is about 1 minute, and the K in the mixed solution 2 Cr 2 o 7 The concentration is 0.3mol / L, the concentration of sulfuric acid is 4mol / L, and the treatment temperature is 60°C. After washing with alkaline water, d...
Embodiment 3
[0035] (1) Preparation of polypropylene fiber: take drawing-grade polypropylene brand-new pellets as ingredients, add appropriate compatibilizer to polypropylene, and add compound antioxidant to the ingredients, and the compound antioxidant is determined by mass fraction 28% of antioxidant 1010, 12% of antioxidant 1024, 23% of Omnistab 46, and 15% of antioxidant 2246 were used to obtain polypropylene fibers, and the oxidation induction time of polypropylene fibers was greater than 30 minutes.
[0036] (2) Surface carboxylation of polypropylene fibers: The monofilament of polypropylene (PP) fibers is drawn through a three-roller winder through a certain temperature of K 2 Cr 2 o 7 and sulfuric acid mixed solution, the time of PP fiber monofilament in the mixed solution is about 1 minute, and the Na in the mixed solution 2 Cr 2 o 7 The concentration is 0.2mol / L, the concentration of sulfuric acid is 1mol / L, and the treatment temperature is 70°C. After washing with alkaline w...
PUM
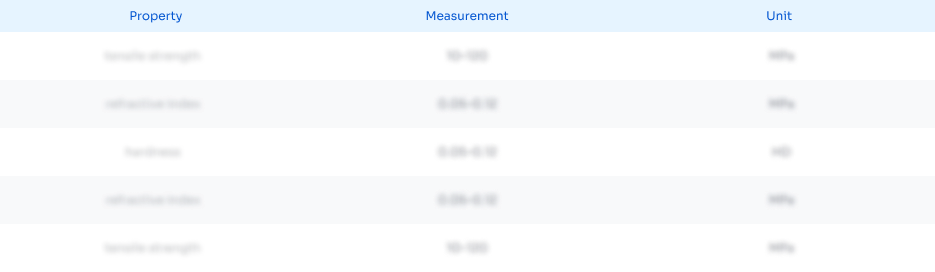
Abstract
Description
Claims
Application Information

- R&D
- Intellectual Property
- Life Sciences
- Materials
- Tech Scout
- Unparalleled Data Quality
- Higher Quality Content
- 60% Fewer Hallucinations
Browse by: Latest US Patents, China's latest patents, Technical Efficacy Thesaurus, Application Domain, Technology Topic, Popular Technical Reports.
© 2025 PatSnap. All rights reserved.Legal|Privacy policy|Modern Slavery Act Transparency Statement|Sitemap|About US| Contact US: help@patsnap.com