A spent fuel storage b 4 Edge-flexible confinement rolling method of c/al composite sheet
A composite material and spent fuel technology, which is applied in the field of flexible constrained rolling of B4C/Al composite sheet edges for spent fuel storage, can solve the problems of reduced material utilization, poor plasticity and toughness, and increased production costs, and achieve a reduction in cost. The effect of reducing the number of times, reducing cracking, and improving production efficiency
- Summary
- Abstract
- Description
- Claims
- Application Information
AI Technical Summary
Problems solved by technology
Method used
Image
Examples
Embodiment 1
[0052] 31wt.%B 4 C / 6061Al composite material, the specific steps are as follows.
[0053] 1. Cold compact preparation: 31wt.%B 4 The powders of the various components of the C / 6061Al composite material are mixed according to the designed composition ratio, and then cold-pressed blanks of the composite material are prepared by cold isostatic pressing.
[0054] 2. Assembling inside the sheath: Assemble the cold compact of the composite material prepared in step 1 into the hot isostatic pressing iron sheath, and place 6061Al alloy strips on both sides and the space of the sheath to form aluminum cladding on both sides of the cold compact. structured as figure 1 shown.
[0055] 3. Hot isostatic pressing: put the package assembled in step 2 into the hot isostatic pressing furnace body, the hot isostatic pressing temperature is 610°C, the pressure is 10 MPa, and the holding time is 5 minutes to prepare a composite material blank with aluminum on the side.
[0056] 4. Billet pret...
Embodiment 2
[0060] 10wt.%B was prepared by using 2024Al as the side cladding aluminum material 4 C / 2024Al composite material, the specific steps are as follows.
[0061] 1. Preparation of cold-pressed blanks: Mix the powders of each component of the composite material according to the designed composition ratio, and then prepare the cold-pressed blanks of the composite material by cold isostatic pressing.
[0062] 2. Assembling in the sheath: Assemble the cold compact of composite material prepared in step 1 into the hot isostatic pressing iron sheath, and place 2024Al alloy strips on both sides and the space of the sheath to form aluminum cladding on both sides of the cold compact. structured as figure 1 shown.
[0063] 3. Hot isostatic pressing: put the package assembled in step 2 into the hot isostatic pressing furnace body, the hot isostatic pressing temperature is 500°C, the pressure is 50 MPa, and the holding time is 30 minutes to prepare a composite material blank with aluminum o...
Embodiment 3
[0068] 45wt.%B was prepared by using 1060Al as the side cladding aluminum material 4 C / 1060Al composite material, the specific steps are as follows.
[0069] 1. Preparation of cold-pressed blanks: Mix the powders of each component of the composite material according to the designed composition ratio, and then prepare the cold-pressed blanks of the composite material by cold isostatic pressing.
[0070] 2. Assembling inside the sheath: Assemble the cold compact of the composite material prepared in step 1 into the hot isostatic pressing iron sheath, and place 1060Al alloy strips on both sides and the space of the sheath to form aluminum cladding on both sides of the cold compact. structured as figure 1 shown.
[0071] 3. Hot isostatic pressing: put the package assembled in step 2 into the hot isostatic pressing furnace body, the hot isostatic pressing temperature is 650°C, the pressure is 30 MPa, and the holding time is 15 minutes, to prepare a composite material blank with a...
PUM
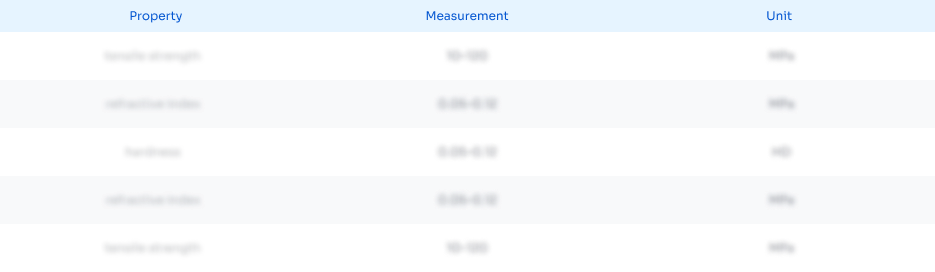
Abstract
Description
Claims
Application Information

- R&D Engineer
- R&D Manager
- IP Professional
- Industry Leading Data Capabilities
- Powerful AI technology
- Patent DNA Extraction
Browse by: Latest US Patents, China's latest patents, Technical Efficacy Thesaurus, Application Domain, Technology Topic, Popular Technical Reports.
© 2024 PatSnap. All rights reserved.Legal|Privacy policy|Modern Slavery Act Transparency Statement|Sitemap|About US| Contact US: help@patsnap.com