Adjustable magnetic valve
A solenoid valve, adjustable technology, applied in the field of solenoid valves, can solve problems such as costly adjustment process
- Summary
- Abstract
- Description
- Claims
- Application Information
AI Technical Summary
Problems solved by technology
Method used
Image
Examples
Embodiment Construction
[0022] as by Figure 1 to Figure 5 As shown, the illustrated embodiments of adjustable solenoid valves 10A, 10B, 10C, 10D, 10E according to the present invention respectively include a magnet assembly 20A, 20B, 20C, 20D, 20E and a guide sleeve 13A, 13B, 13C, 13D, 13E, the immovable part 11 is fixedly arranged in said guide sleeve and the valve armature 17A, 17B, 17C, 17D, 17E can overcome the force of the return spring 16A, 16B, 16C, 16D, 16E The force is arranged axially displaceable in the guide sleeve. The magnet assembly 20A, 20B, 20C, 20D, 20E is pushed onto the immovable part 11 formed for the valve and the guide sleeve 13A, 13B, 13C, 13D, 13E. Axial stops of the armatures 17A, 17B, 17C, 17D, 17E. Said valve armatures 17A, 17B, 17C, 17D, 17E are actuatable by magnetic forces generated by energized magnet assemblies 20A, 20B, 20C, 20D, 20E, and during movement in the blocking direction move the blocking elements 17.1A, 17.1B . D, 17.1E are lifted from valve seats 15.1...
PUM
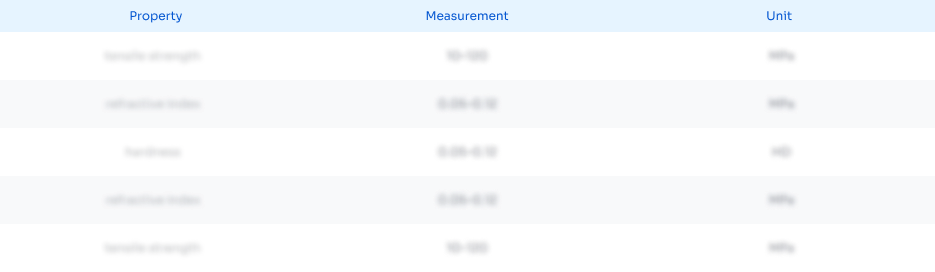
Abstract
Description
Claims
Application Information

- Generate Ideas
- Intellectual Property
- Life Sciences
- Materials
- Tech Scout
- Unparalleled Data Quality
- Higher Quality Content
- 60% Fewer Hallucinations
Browse by: Latest US Patents, China's latest patents, Technical Efficacy Thesaurus, Application Domain, Technology Topic, Popular Technical Reports.
© 2025 PatSnap. All rights reserved.Legal|Privacy policy|Modern Slavery Act Transparency Statement|Sitemap|About US| Contact US: help@patsnap.com