End part structure of antiroll torsion bar capable of preventing galvanic corrosion
An anti-rolling torsion bar, galvanic corrosion technology, applied in the direction of railway car body parts, bogies, axle self-adjustment, etc. The effect of reducing maintenance costs
- Summary
- Abstract
- Description
- Claims
- Application Information
AI Technical Summary
Problems solved by technology
Method used
Image
Examples
Embodiment 1
[0043] Embodiment 1: as Figure 7 and Figure 8 As shown, an anti-rolling torsion bar end structure to prevent galvanic corrosion, which includes a coating 6 sprayed on the outer peripheral surface of the torsion bar end 312, the coating 6 is located at the end of the torsion bar after assembly 312 and the position between the torsion bar bearing 2, use the coating 6 to prevent direct contact of different materials and prevent the formation of a current loop and the main sealing ring 7 arranged between the torsion bar end face 311 of the torsion bar and the torsion bar bearing end face 211, use The torsion bar bearing end surface 211 presses the main sealing ring 7 onto the torsion bar end surface 311 of the torsion bar, so that a sealed fitting surface is formed on the torsion bar bearing end surface 211, preventing external electrolyte from entering the torsion bar bearing, Thereby preventing the occurrence of galvanic corrosion. In this embodiment, the coating is applied ...
Embodiment 2
[0057] Embodiment 2: The applicant conducted further research on the possibility of failure of the sealing performance of the spline joint between the torsion bar and the torsion arm through various tests and spline sealing performance analysis.
PUM
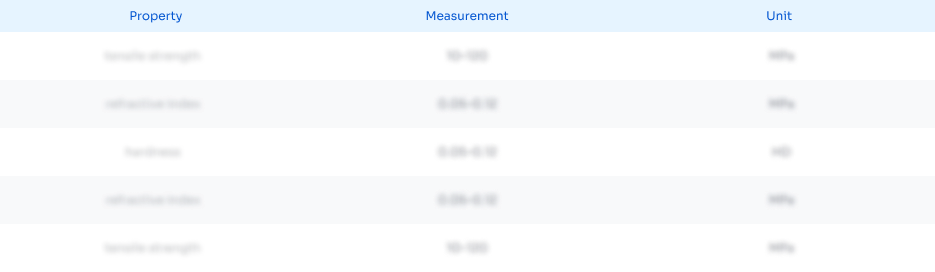
Abstract
Description
Claims
Application Information

- R&D
- Intellectual Property
- Life Sciences
- Materials
- Tech Scout
- Unparalleled Data Quality
- Higher Quality Content
- 60% Fewer Hallucinations
Browse by: Latest US Patents, China's latest patents, Technical Efficacy Thesaurus, Application Domain, Technology Topic, Popular Technical Reports.
© 2025 PatSnap. All rights reserved.Legal|Privacy policy|Modern Slavery Act Transparency Statement|Sitemap|About US| Contact US: help@patsnap.com