Suspension system and whole backpack-type mobile robot
A mobile robot and suspension system technology, applied in the field of mobile robots, can solve the problems of driving wheel slippage, limited carrying capacity, easy to slip, etc., and achieve the effect of compact overall structure, small volume and space, and high transmission efficiency.
- Summary
- Abstract
- Description
- Claims
- Application Information
AI Technical Summary
Problems solved by technology
Method used
Image
Examples
Embodiment Construction
[0043] The application will be further described below in conjunction with the accompanying drawings and specific embodiments, so that those skilled in the art can better understand the application and implement it, but the examples given are not intended to limit the application.
[0044] See attached Figures 1 to 18 , a suspension system described in a preferred embodiment of the present description and a full backpack mobile robot with the suspension system, wherein, the full backpack mobile robot includes a frame 14 and a suspension at the bottom of the frame 14 system, the suspension system includes two suspension mechanisms arranged left and right: respectively the left suspension mechanism 7 arranged on the left side of the vehicle frame 14 and the right suspension mechanism 9 arranged on the right side of the vehicle frame 14, in order to ensure the The full backpack mobile robot can adapt to different road conditions and adapt to different loads. Each suspension mech...
PUM
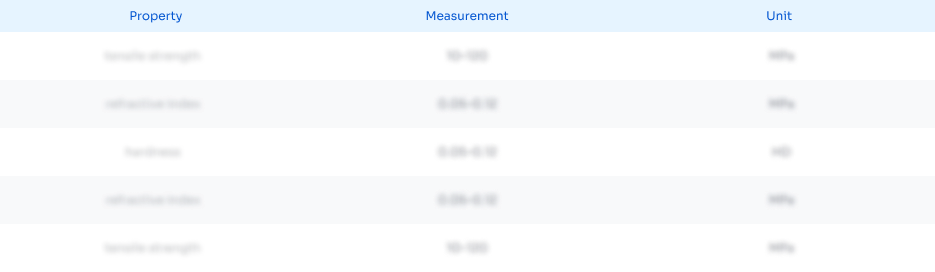
Abstract
Description
Claims
Application Information

- R&D Engineer
- R&D Manager
- IP Professional
- Industry Leading Data Capabilities
- Powerful AI technology
- Patent DNA Extraction
Browse by: Latest US Patents, China's latest patents, Technical Efficacy Thesaurus, Application Domain, Technology Topic, Popular Technical Reports.
© 2024 PatSnap. All rights reserved.Legal|Privacy policy|Modern Slavery Act Transparency Statement|Sitemap|About US| Contact US: help@patsnap.com