A kind of biodegradable non-woven fabric and preparation method thereof
A biodegradable, non-woven technology, used in electrospinning, non-woven fabrics, textiles and papermaking, etc., can solve problems such as spinning difficulties, achieve good mechanical properties and fresh-keeping properties, reduce costs, and have a wide range of effects.
- Summary
- Abstract
- Description
- Claims
- Application Information
AI Technical Summary
Problems solved by technology
Method used
Image
Examples
Embodiment 1
[0059] The preparation of embodiment 1 biodegradable non-woven fabric
[0060] Raw material composition:
[0061] 70 parts of acrylic acid modified corn bran fiber;
[0062] 30 parts of abaca leaves;
[0063] 20 parts of ofloxacin;
[0064] Silane coupling agent DL1715 parts;
[0065] Tween 5 parts;
[0066] 1 part of 2,2'-thiobis(4-tert-octylphenoxy)nickel;
[0067] 1 part of resorcinol monobenzoate;
[0068] Polysorbate 801 parts;
[0069] 5 parts of decabromo-antimony trioxide;
[0070] 5 parts of tetrakis [β-(3,5-tertiary butyl-4-hydroxyphenyl) propionate] pentaerythritol ester;
[0071] 5 parts of diethyl phthalate.
[0072] Preparation of acrylic acid modified corn husk fiber: Wash the corn husk fiber, dry it in the sun, heat and dissolve it in a mixed solvent of toluene and n-butanol (4:1 by volume), add n-dodecanethiol, remove oxygen for 30 minutes, Introduce argon, continue to add methyl methacrylate, ethyl acrylate, butyl acrylate and acrylonitrile monomers...
Embodiment 2
[0074] The preparation of embodiment 2 biodegradable non-woven fabrics
[0075] Raw material composition:
[0076] 100 parts of acrylic acid modified corn bran fiber;
[0077] 50 parts of willow seed hair;
[0078] 30 parts of ofloxacin;
[0079] Silane coupling agent DL17115 parts;
[0080] Tween 10 parts;
[0081] 5 parts of 2,2'-thiobis(4-tert-octylphenoxy)nickel;
[0082] 5 parts of resorcinol monobenzoate;
[0083] Polysorbate 8010 parts;
[0084] 10 parts of hexabromocyclododecane;
[0085] 15 parts of three (dodecyl alcohol) esters;
[0086] 10 parts of diisodecyl phthalate.
[0087] Preparation of acrylic acid modified corn husk fiber: Wash the corn husk fiber, dry it in the sun, heat and dissolve it in a mixed solvent of toluene and n-butanol (4:1 by volume), add n-dodecanethiol, remove oxygen for 30 minutes, Introduce argon, continue to add methyl methacrylate, ethyl acrylate, butyl acrylate and acrylonitrile monomers, under the trigger of the initiator azo...
Embodiment 3
[0089] The preparation of embodiment 3 biodegradable non-woven fabrics
[0090] Raw material composition:
[0091] 80 parts of acrylic acid modified corn bran fiber;
[0092] 45 parts jute stalks;
[0093] Ofloxacin 27 parts;
[0094] Silane coupling agent DL17112 parts;
[0095] Tween 8 parts;
[0096] 4 parts of 2,2'-thiobis(4-tert-octylphenoxy)nickel;
[0097] 4 parts of resorcinol monobenzoate;
[0098] Polysorbate 808 parts;
[0099] 8 parts of flame retardant MCA;
[0100] 12 parts of diphenylamine;
[0101] 9 parts of butyl benzyl phthalate.
[0102] Preparation of acrylic acid modified corn husk fiber: Wash the corn husk fiber, dry it in the sun, heat and dissolve it in a mixed solvent of toluene and n-butanol (4:1 by volume), add n-dodecanethiol, remove oxygen for 30 minutes, Introduce argon, continue to add methyl methacrylate, ethyl acrylate, butyl acrylate and acrylonitrile monomers, under the trigger of the initiator azobisisobutyronitrile, heat to 90 ° ...
PUM
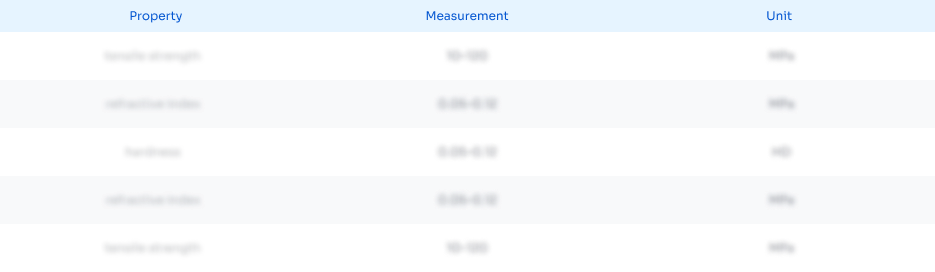
Abstract
Description
Claims
Application Information

- Generate Ideas
- Intellectual Property
- Life Sciences
- Materials
- Tech Scout
- Unparalleled Data Quality
- Higher Quality Content
- 60% Fewer Hallucinations
Browse by: Latest US Patents, China's latest patents, Technical Efficacy Thesaurus, Application Domain, Technology Topic, Popular Technical Reports.
© 2025 PatSnap. All rights reserved.Legal|Privacy policy|Modern Slavery Act Transparency Statement|Sitemap|About US| Contact US: help@patsnap.com