Automatic casting coating spraying device
A technology of automatic spraying and feeding device, applied in spraying device, spray booth, etc., can solve the problems of reducing product quality, uneven spraying, adhesion to the barrel wall, etc., to improve spraying effect, speed up mixing speed, and spraying work. easy effect
- Summary
- Abstract
- Description
- Claims
- Application Information
AI Technical Summary
Problems solved by technology
Method used
Image
Examples
Embodiment Construction
[0026] The following will clearly and completely describe the technical solutions in the embodiments of the present invention with reference to the accompanying drawings in the embodiments of the present invention. Obviously, the described embodiments are only some, not all, embodiments of the present invention.
[0027] refer to Figure 1-7 , an automatic coating device for castings, including a base 1, the lower end of the base 1 is symmetrically provided with rollers 8, which can facilitate the overall movement of the device and facilitate the movement and transportation of the device.
[0028] The upper end of the base 1 is provided with a working box 2, and one side of the working box 2 is provided with a mixing device 3, and the mixing device 3 includes a paint box 31 fixedly connected with the working box 2, and both sides of the upper end of the paint box 31 are respectively provided with a liquid inlet Port 32, a stirring motor 33 is installed in the middle part of th...
PUM
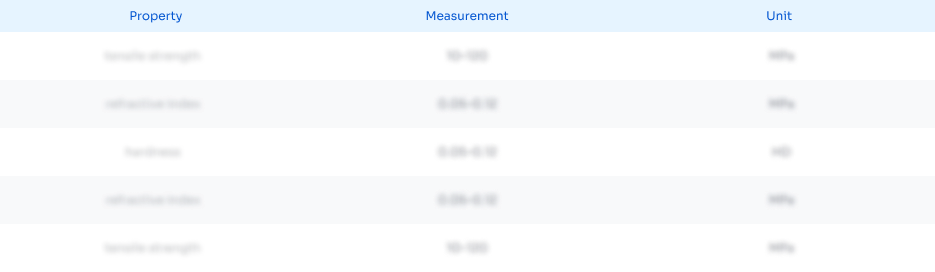
Abstract
Description
Claims
Application Information

- R&D Engineer
- R&D Manager
- IP Professional
- Industry Leading Data Capabilities
- Powerful AI technology
- Patent DNA Extraction
Browse by: Latest US Patents, China's latest patents, Technical Efficacy Thesaurus, Application Domain, Technology Topic, Popular Technical Reports.
© 2024 PatSnap. All rights reserved.Legal|Privacy policy|Modern Slavery Act Transparency Statement|Sitemap|About US| Contact US: help@patsnap.com