Hot forming process of train wheel with large difference between reverse spoke plate and rim plate distance
A hot forming and train technology, applied in the direction of spoked wheels, wheels, vehicle parts, etc., can solve the problems of too large gap between rims, difficult processing, easy to produce defects, etc., so as to reduce the possibility of production and improve the hot forming. The effect of pass rate
- Summary
- Abstract
- Description
- Claims
- Application Information
AI Technical Summary
Problems solved by technology
Method used
Image
Examples
Embodiment Construction
[0025] The specific embodiment of the present invention will be described in further detail by describing the embodiments below with reference to the accompanying drawings. The purpose is to help those skilled in the art to have a more complete, accurate and in-depth understanding of the inventive concept and technical solutions of the present invention. and contribute to its implementation.
[0026] Such as Figure 1 to Figure 4 As shown, the present invention provides a train wheel thermoforming process with a large difference in the distance between the rim and plate of the anti-spoke plate, including a preforming step, a forming step, a rolling step and a bending step. In the rolling step, the left The web roller 23 and the right web roller 22 cooperate to roll the forming blank, the right web roller 22 has the first working surface 2201 of the right roller and the second working surface 2202 of the right roller, and the first working surface 2201 of the right roller and t...
PUM
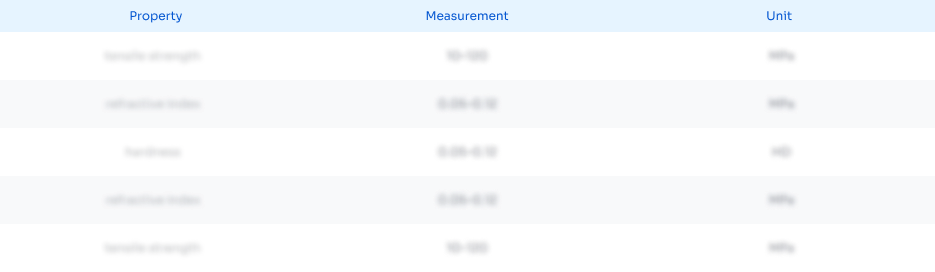
Abstract
Description
Claims
Application Information

- R&D
- Intellectual Property
- Life Sciences
- Materials
- Tech Scout
- Unparalleled Data Quality
- Higher Quality Content
- 60% Fewer Hallucinations
Browse by: Latest US Patents, China's latest patents, Technical Efficacy Thesaurus, Application Domain, Technology Topic, Popular Technical Reports.
© 2025 PatSnap. All rights reserved.Legal|Privacy policy|Modern Slavery Act Transparency Statement|Sitemap|About US| Contact US: help@patsnap.com