Coal tar hydrodemetallization catalyst and preparation method thereof
A hydrodemetallization and catalyst technology, which is applied in the direction of catalyst activation/preparation, chemical instruments and methods, physical/chemical process catalysts, etc., can solve the problems of cumbersome steps and secondary pollution, and achieve the effect of reducing surface tension
- Summary
- Abstract
- Description
- Claims
- Application Information
AI Technical Summary
Benefits of technology
Problems solved by technology
Method used
Examples
preparation example Construction
[0050] The preparation method of coal tar hydrogenation demetallization catalyst support comprises the following steps:
[0051] A. Weigh 73% to 91% of dry aluminum hydroxide powder, 2% to 6% of lubricant, 5% to 15% of pore expanding agent and 2% to 6% of sintering agent in proportion, add 100% to 150% of water and knead Uniform post-extrusion molding;
[0052] B. Using freeze-drying, through three stages of freezing, sublimation and re-drying, adjust the temperature and pressure in the freeze-drying process, control the step-by-step release of water, and gradually remove the surface water and bound water in the carrier. The freezing temperature is -25°C ~-35°C, freezing pressure 8pa~12pa; control freeze-drying oven temperature -55°C--65°C during sublimation, freeze-drying oven pressure 1pa-3pa, shelf temperature 10°C-30°C; re-drying temperature 25°C-35 ℃;
[0053] C. Preparation and roasting of the alumina carrier. The heating rate is controlled at 20°C / h to 25°C / h, the tempe...
Embodiment 1
[0060] ① Preparation of alumina carrier. Weigh 500g of aluminum hydroxide dry glue, 7g of turnip powder, 7g of ammonium oxalate, and 18g of kaolin, and add them to the dry mixer. Extrusion machine extrusion molding, put the formed material into the cold storage to cool to 2°C, and then place it in a freeze-drying box with a pressure of -30°C and a pressure of 10Pa to freeze the formed material quickly, and reduce the temperature and pressure in the freeze-drying box to -60 ℃ pressure 2Pa, control shelf temperature 10 ℃, when the water vapor from the sublimation of ice in the material in the vacuum system no longer flows out, then raise the shelf to 30 ℃ to re-dry the material, and discharge the water vapor in the vacuum system The water in the condenser removes the bound water in the material. After drying, control the heating rate of 25°C / h, and control the temperature of 520°C for 4h in a calcination furnace to obtain an alumina carrier.
[0061] ② Catalyst preparation. W...
Embodiment 2
[0063] ① Preparation of alumina carrier. Weigh 500g of aluminum hydroxide dry glue, 7g of starch, 7g of urea, and 18g of attapulgite into a dry mixer, dry mix evenly, slowly add 750g of pure water, knead and roll, roll into a plastic body, and then squeeze The strip machine is extruded into strips, put the formed material into the cold storage to cool to 2°C, and then put it in the -30°C (10Pa) freeze-drying box to freeze the formed material quickly, and reduce the temperature and pressure in the freeze-drying box to -60 ℃ and 2Pa, control the temperature of the shelf at 10℃, and when the water vapor from the sublimation of ice in the material in the vacuum system no longer flows out, raise the shelf to 30℃ for re-drying of the material, and discharge the water vapor in the vacuum system The water in the condenser removes the bound water in the material. After drying, the heating rate was controlled at 20°C / h, and the temperature was controlled at 520°C for 6 hours in a roast...
PUM
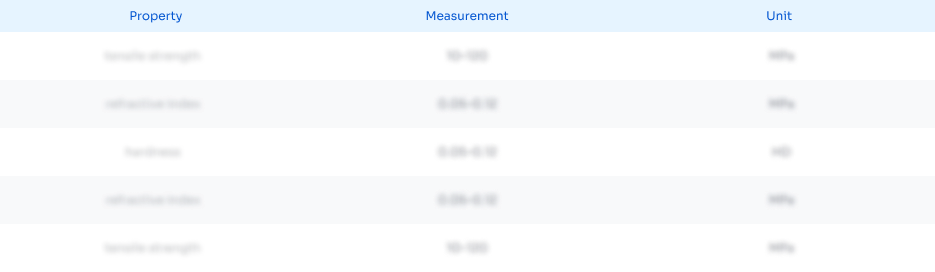
Abstract
Description
Claims
Application Information

- R&D Engineer
- R&D Manager
- IP Professional
- Industry Leading Data Capabilities
- Powerful AI technology
- Patent DNA Extraction
Browse by: Latest US Patents, China's latest patents, Technical Efficacy Thesaurus, Application Domain, Technology Topic, Popular Technical Reports.
© 2024 PatSnap. All rights reserved.Legal|Privacy policy|Modern Slavery Act Transparency Statement|Sitemap|About US| Contact US: help@patsnap.com