System and method for synchronously controlling fatigue loading of wind turbine blades based on multiple exciters
A wind turbine blade and fatigue loading technology, which is applied in the direction of mechanical oscillation control, control/regulation system, electric controller, etc., can solve the problem of low vibration excitation ability, improve adaptability and robustness, improve accuracy and The effect of excitation ability
- Summary
- Abstract
- Description
- Claims
- Application Information
AI Technical Summary
Problems solved by technology
Method used
Image
Examples
Embodiment Construction
[0032] In order to deepen the understanding of the present invention, the following will be described in detail in conjunction with the accompanying drawings and specific embodiments. The embodiments described in this specification are only used to explain the present invention, and are not intended to limit the present invention.
[0033] figure 1 As shown, the wind turbine blade multi-exciter synchronous fatigue loading control system of the present invention, its hardware includes a host computer and a lower computer, the upper and lower computers are based on Ethernet communication, and the upper computer has a frequency search and tracking module, a sensor detection module , data recording module and Labview communication module, connected to the laser rangefinder through RS485, and based on Ethernet communication with the strain tester, the upper computer is a man-machine interface written by Labview, the main functions include operating parameter setting and display, and...
PUM
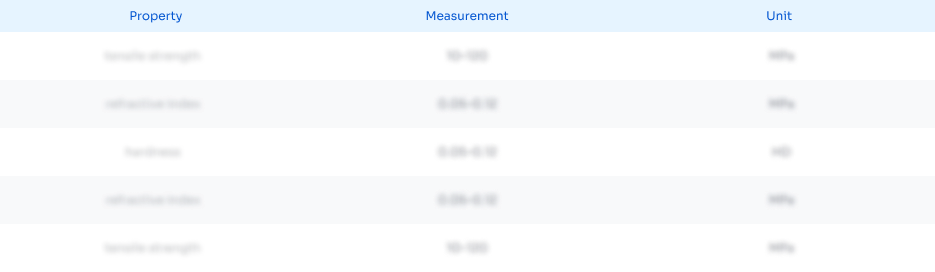
Abstract
Description
Claims
Application Information

- R&D Engineer
- R&D Manager
- IP Professional
- Industry Leading Data Capabilities
- Powerful AI technology
- Patent DNA Extraction
Browse by: Latest US Patents, China's latest patents, Technical Efficacy Thesaurus, Application Domain, Technology Topic, Popular Technical Reports.
© 2024 PatSnap. All rights reserved.Legal|Privacy policy|Modern Slavery Act Transparency Statement|Sitemap|About US| Contact US: help@patsnap.com