Small aero-engine multi-point rubbing fault simulation experiment device
An aero-engine and experimental device technology, applied in the field of aero-engines, can solve problems such as difficult simulation, large differences in rubbing failures, and inability to simulate engine working conditions, and achieve the effect of ensuring safety and ensuring safety.
- Summary
- Abstract
- Description
- Claims
- Application Information
AI Technical Summary
Problems solved by technology
Method used
Image
Examples
Embodiment Construction
[0031] The present invention will be described in detail below in conjunction with the accompanying drawings and specific embodiments.
[0032] Such as figure 1 — Figure 6 As shown, the small aeroengine multi-point rubbing fault simulation experiment device provided by the present invention includes a rotor system, a rubbing system, a drive system, a support system and a measurement and control system;
[0033] Wherein the supporting system comprises left bearing seat 20, right bearing seat 7, left sensor support 3, middle sensor support 6, right sensor support 9, test bench base 18 and damping support 19; described test bench base 18 is horizontally arranged , a vibration-damping support 19 is respectively installed at the four corners of the bottom surface; the left sensor bracket 3, the left bearing seat 20, the middle sensor bracket 6, the right bearing seat 7 and the right sensor bracket 9 are installed on the base of the test bench at intervals from left to right 18 i...
PUM
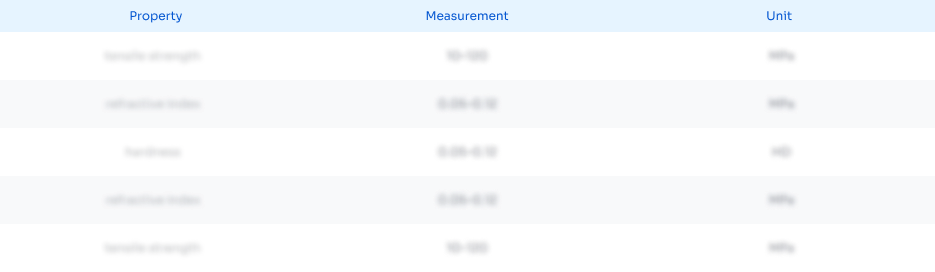
Abstract
Description
Claims
Application Information

- R&D
- Intellectual Property
- Life Sciences
- Materials
- Tech Scout
- Unparalleled Data Quality
- Higher Quality Content
- 60% Fewer Hallucinations
Browse by: Latest US Patents, China's latest patents, Technical Efficacy Thesaurus, Application Domain, Technology Topic, Popular Technical Reports.
© 2025 PatSnap. All rights reserved.Legal|Privacy policy|Modern Slavery Act Transparency Statement|Sitemap|About US| Contact US: help@patsnap.com