Improved Soldering Method for Aluminum Enameled Wire of Terminals of Motor Coil Assembly and Drainage Pump
A technology for aluminum enameled wires and terminals, which is applied in the field of motors using aluminum enameled wires, can solve problems such as difficult automatic cleaning and quality fluctuations, and achieve excellent tin climbing performance, ensure wettability, and excellent adhesion performance.
- Summary
- Abstract
- Description
- Claims
- Application Information
AI Technical Summary
Problems solved by technology
Method used
Image
Examples
Embodiment Construction
[0029] An improved soldering method for aluminum enameled wire of a motor of the present invention comprises the following steps:
[0030] (1) if figure 1 As shown, the aluminum enameled wire 2 is wound on the terminal 1 by using an automatic winding machine, and there is a wire gap between adjacent aluminum enameled wires 2 that can accommodate the copper enameled wire; preferably, the wire gap is larger than the wire of the copper enameled wire The diameter of copper enameled wire can be 0.06-0.1mm.
[0031] (2) if figure 2 As shown, a copper enameled wire 3 is wound on the outer surface of the aluminum enameled wire wound on the terminal, and the copper enameled wire 3 fills the gap between adjacent aluminum enameled wires. Except for the side contacting the terminal, each aluminum enameled wire The remaining outer surfaces are in contact with the copper enameled wire and are completely wrapped in the copper enameled wire; in this step, the winding of the copper enameled...
PUM
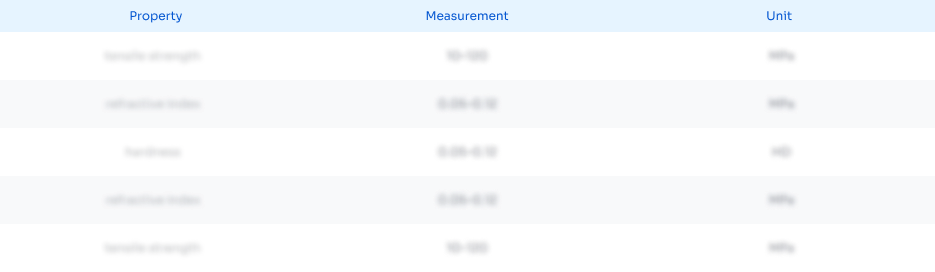
Abstract
Description
Claims
Application Information

- R&D
- Intellectual Property
- Life Sciences
- Materials
- Tech Scout
- Unparalleled Data Quality
- Higher Quality Content
- 60% Fewer Hallucinations
Browse by: Latest US Patents, China's latest patents, Technical Efficacy Thesaurus, Application Domain, Technology Topic, Popular Technical Reports.
© 2025 PatSnap. All rights reserved.Legal|Privacy policy|Modern Slavery Act Transparency Statement|Sitemap|About US| Contact US: help@patsnap.com