A side wall forming mold and a side wall forming process
A technology of forming mold and forming process, applied in the field of car body, can solve problems such as aluminum plate cracking, and achieve the effect of avoiding cracking
- Summary
- Abstract
- Description
- Claims
- Application Information
AI Technical Summary
Problems solved by technology
Method used
Image
Examples
Embodiment 1
[0048] The embodiment of the present invention provides a side wall forming die. The side wall forming die includes an upper die body 1 , a lower die base 2 , a punch 3 arranged on the lower die base 2 , and a compensation tool movably arranged on the upper die body 1 . The concave die 4, the inner crimping ring 5 which is movable inside the punch 3 and matched with the pressing surface of the compensating die 4, and the outer crimping ring 6 which is movable and arranged outside the punch 3; the inner crimping The ring 5 is provided with an inner secondary ejector pin 7, and the outer edge holder ring 6 is provided with an outer secondary ejector pin 8; wherein: the length of the inner secondary ejector pin 7 is less than the length of the outer secondary ejector pin 8, and the die In the closed state, the lower end face of the inner secondary ejector rod 7 is higher than the lower end face of the outer secondary ejector rod 8 by Δh; the upper mold body 1 is also provided with...
Embodiment 2
[0055] The present embodiment provides a side wall forming process, wherein: the above side wall forming die is used to carry out side wall drawing forming. The inner edge holder 5 has only one limit position. When it is specifically implemented, the side wall forming process is as follows: Figure 8 shown, including the following steps:
[0056] Step S10: First, the upper die body 1 and the punch 3 are in the mold-opening state; then, the machine tool ejector 9 goes up, and the machine tool ejector 9 first contacts the outer secondary ejector bar 8 and lifts 6, and then the machine tool ejector 9 goes up again. Contact the inner secondary ejector rod 7 and lift up the inner edge holder 5, so that the inner side holder 5 and the outer side holder 6 move to the same height, and the upper surfaces of the inner side holder 5 and the outer side holder 6 are formed at this time. Smooth and smooth lower pressing surface, the lower pressing surface is higher than punch 3, such as ...
Embodiment 3
[0067] The present embodiment provides a side wall forming process, wherein: using the above side wall forming die to carry out side wall drawing forming, the difference between this embodiment and Embodiment 2 is that in this embodiment, the inner edge holder 5 At the same time, the lower mold nitrogen gas spring and the lower mold base 2 are used to limit the position respectively. At this time, it is required to set the lower mold nitrogen gas spring to provide driving force and pressure source in the lower mold; set the stroke and force of the lower mold nitrogen gas spring, and the lower mold nitrogen gas spring The force can be used as the pressure source of the inner edge holder 5 to limit the inner edge holder 5 during the mold clamping process, and the stroke of the lower die nitrogen gas spring can be used as the elastic stroke of the inner edge holder 5, while the lower die seat 2 pairs of inner blank holder 5 provide rigid limit. During the clamping process, the co...
PUM
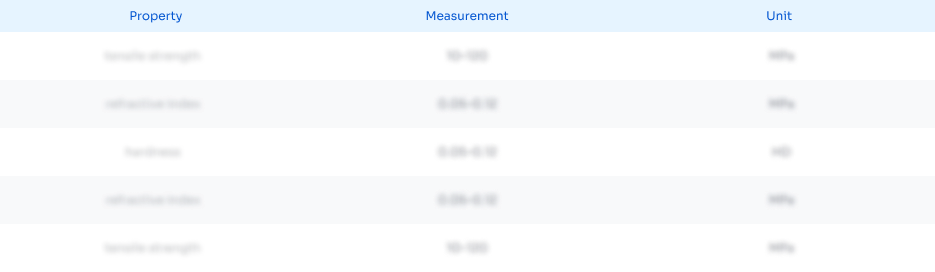
Abstract
Description
Claims
Application Information

- R&D Engineer
- R&D Manager
- IP Professional
- Industry Leading Data Capabilities
- Powerful AI technology
- Patent DNA Extraction
Browse by: Latest US Patents, China's latest patents, Technical Efficacy Thesaurus, Application Domain, Technology Topic, Popular Technical Reports.
© 2024 PatSnap. All rights reserved.Legal|Privacy policy|Modern Slavery Act Transparency Statement|Sitemap|About US| Contact US: help@patsnap.com