Stamping and drawing forming process of fender
A molding process and fender technology, applied in transportation and packaging, vehicle parts, etc., can solve the problems of increased manufacturing cost, low material utilization rate, deep molding depth, etc., to reduce waste, reduce the risk of strain, and improve material quality. The effect of utilization
- Summary
- Abstract
- Description
- Claims
- Application Information
AI Technical Summary
Problems solved by technology
Method used
Image
Examples
Embodiment Construction
[0018] see figure 1 The finished fender includes the outer surface 1 displayed on the surface of the car body, the connecting surface 2 that is turned over the edge of the outer surface 1 and connected with the adjacent car body parts, and the joint connecting surface that extends from the connecting surface 2 and the car body Component mounting bracket 3.
[0019] see figure 2 , the material utilization rate of the fender part is mainly determined by the extension length of the mounting bracket. The extension length of the outer surface 1, the connecting surface 2, and the traditional mounting bracket 03 out of the plane is far greater than that of other areas of the drawn profile. After the process, the process supplementary surface outside the outer surface 1, the connecting surface 2 and the traditional mounting bracket 03 area (outside the trimming line 5) will become waste, so how to reduce the drawing depth of the outer surface, connecting surface and mounting bracket...
PUM
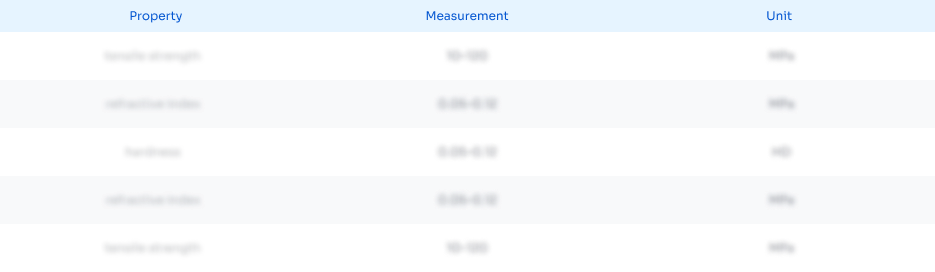
Abstract
Description
Claims
Application Information

- Generate Ideas
- Intellectual Property
- Life Sciences
- Materials
- Tech Scout
- Unparalleled Data Quality
- Higher Quality Content
- 60% Fewer Hallucinations
Browse by: Latest US Patents, China's latest patents, Technical Efficacy Thesaurus, Application Domain, Technology Topic, Popular Technical Reports.
© 2025 PatSnap. All rights reserved.Legal|Privacy policy|Modern Slavery Act Transparency Statement|Sitemap|About US| Contact US: help@patsnap.com