Metal smelting and pouring system
A pouring system and metal technology, applied in metal processing equipment, equipment for sending molten metal into molds, mechanical cleaning, etc., can solve problems such as rough surface of ingots, failure to use normally, miscellaneous inclusions, etc., to achieve good transportation and Processing function, ensuring the quality of ingot, and the effect of good processing effect
- Summary
- Abstract
- Description
- Claims
- Application Information
AI Technical Summary
Problems solved by technology
Method used
Image
Examples
Embodiment 2
[0026] Example 2 is as Figure 5 As shown, the input port of the buffer tank (the output port of the backflow purification pit 5 ) is not provided with a ceramic filter screen plate. The remaining structures and corresponding purification treatment methods of this example can be similar to those of the above-mentioned embodiment.
Embodiment 3
[0027] Example 3 is as Image 6 shown. The buffer tank 2 is connected with a pouring tank 9, and the output port of the buffer tank 2 is an undercurrent wide-mouth output port 6 arranged on one side wall of the pouring tank. The undercurrent wide-mouth type output port is provided with an undercurrent purification device composed of an anti-oxidation isolation baffle 7 and a deposition baffle 8 . The underflow wide-mouth output port is a rectangular opening with the same width as the side wall of the corresponding side of the injection groove (the side of the output port). The anti-oxidation isolation barrier 7 and the deposition barrier 8 are respectively composed of upper and lower side walls of a rectangular opening.
[0028] The anti-oxidation isolation baffle 7 isolates the buffer tank from the pouring tank in gas phase. The deposition block is slightly higher than the bottom wall of the buffer tank. The turbulent purification pit is a semi-blind chamber type turbulen...
Embodiment 4
[0032] In embodiment 4, as Figure 7 As shown, the bottom wall of the backflow purification pit is in a wave shape, the output port of the backflow purification pit 5 is arranged on the corresponding wave crest 15 of the bottom wall surface of the wave shape of the backflow purification pit, and the wave crest output port of the backflow purification pit is provided with a ceramic filter. Stencil 4b. The bottom wall of the output end (output port) of the input runner is provided with an inertial freewheeling device 16, and the inertial freewheeling device extends convexly from the bottom wall of the output port of the input runner in the direction of the backflow purification pit with the original inclination of the bottom plate of the input runner. formed by the protruding part. The intercepting side wall surface 14 of the backflow purification pit on the side facing the input direction of the input flow channel is provided with an extended backflow wall surface inclined opp...
PUM
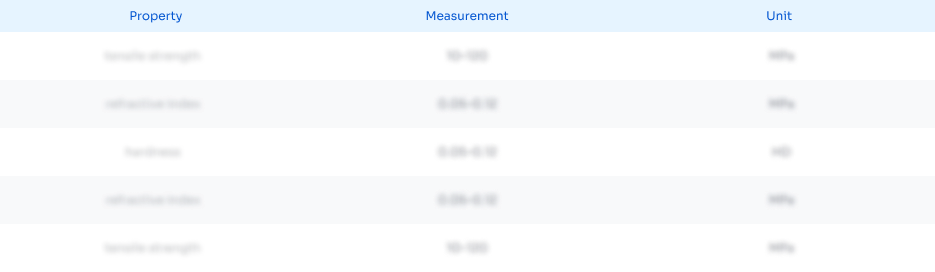
Abstract
Description
Claims
Application Information

- R&D Engineer
- R&D Manager
- IP Professional
- Industry Leading Data Capabilities
- Powerful AI technology
- Patent DNA Extraction
Browse by: Latest US Patents, China's latest patents, Technical Efficacy Thesaurus, Application Domain, Technology Topic, Popular Technical Reports.
© 2024 PatSnap. All rights reserved.Legal|Privacy policy|Modern Slavery Act Transparency Statement|Sitemap|About US| Contact US: help@patsnap.com