Five-shaft structure error measuring method of mirror image milling system, system and device thereof
A technology of mirror milling and error measurement, applied in general control systems, control/adjustment systems, instruments, etc., can solve the problem of inability to mirror motion error measurement and correction
- Summary
- Abstract
- Description
- Claims
- Application Information
AI Technical Summary
Problems solved by technology
Method used
Image
Examples
Embodiment Construction
[0049] Features and exemplary embodiments of various aspects of the invention will be described in detail below. The detailed description and accompanying drawings of the following embodiments are used to illustrate the principles of the present invention, but are not used to limit the scope of the present invention, that is, the present invention is not limited to the described preferred embodiments, and the scope of the present invention is defined by the claims . In the drawings and the following description, at least some of the well-known structures and techniques have not been shown in order to avoid unnecessarily obscuring the present invention. Furthermore, the features, structures, or characteristics described hereinafter may be combined in any suitable manner in one or more embodiments.
[0050] The present invention is researched on a skin mirror milling processing equipment. Aiming at the problem that the CNC milling processing head and the follower support mechan...
PUM
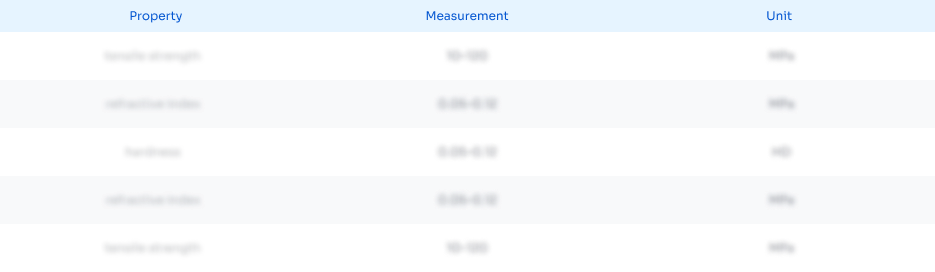
Abstract
Description
Claims
Application Information

- R&D
- Intellectual Property
- Life Sciences
- Materials
- Tech Scout
- Unparalleled Data Quality
- Higher Quality Content
- 60% Fewer Hallucinations
Browse by: Latest US Patents, China's latest patents, Technical Efficacy Thesaurus, Application Domain, Technology Topic, Popular Technical Reports.
© 2025 PatSnap. All rights reserved.Legal|Privacy policy|Modern Slavery Act Transparency Statement|Sitemap|About US| Contact US: help@patsnap.com