White cement clinker bleaching process high in waste heat utilization rate
A utilization rate, white cement technology, applied in the field of white cement bleaching, can solve the problems of no secondary air and tertiary air, heat waste, etc., and achieve the effect of improving the utilization rate
- Summary
- Abstract
- Description
- Claims
- Application Information
AI Technical Summary
Problems solved by technology
Method used
Image
Examples
Embodiment Construction
[0032] Embodiments of the present invention will be further described below in conjunction with the accompanying drawings.
[0033] like Figure 1 to Figure 6 As shown, a white cement clinker bleaching process with high waste heat utilization rate in this embodiment is provided with a material distribution device 2 at the discharge end of the rotary kiln 1, and the two discharge ends of the material distribution device 2 are respectively connected to the grate The feed port of the grate cooler 3 and the feed port of the water-cooled bleaching machine 4, the water-cooled bleaching machine 4 is located directly above the grate cooler 3, and the high-temperature cement clinker discharged from the rotary kiln 1 falls into the material distribution device 2, The distributing device 2 imports 50% of the clinker into the feed port of the water-cooled bleaching machine 4, and the remaining clinker is introduced into the grate cooler 3;
[0034] The high-temperature clinker entering t...
PUM
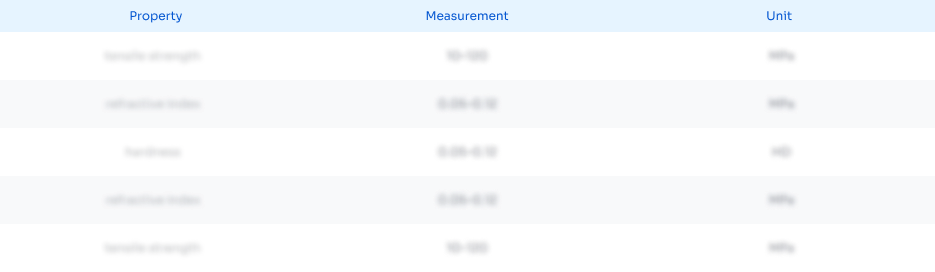
Abstract
Description
Claims
Application Information

- R&D Engineer
- R&D Manager
- IP Professional
- Industry Leading Data Capabilities
- Powerful AI technology
- Patent DNA Extraction
Browse by: Latest US Patents, China's latest patents, Technical Efficacy Thesaurus, Application Domain, Technology Topic, Popular Technical Reports.
© 2024 PatSnap. All rights reserved.Legal|Privacy policy|Modern Slavery Act Transparency Statement|Sitemap|About US| Contact US: help@patsnap.com