Preparation method of flexible strain sensor based on conductive fiber and application thereof
A strain sensor and conductive fiber technology, which is applied in fiber processing, catheters, textiles and papermaking, etc., can solve the problems that the thickness of the conductive coating cannot be accurately controlled, affects the long-term performance of the device, and the conductive particles on the surface of the fiber are easy to fall off. Real-time monitoring of human movement, increasing the detectable range, and promoting the effect of deposition and adsorption
- Summary
- Abstract
- Description
- Claims
- Application Information
AI Technical Summary
Problems solved by technology
Method used
Image
Examples
Embodiment 1
[0035] a. Cleaning of elastic yarn: the internal structure and surface morphology of elastic yarn are as follows: figure 1 As shown in (a), a section of 5 cm long elastic yarn was cut, ultrasonically cleaned in ethanol and deionized water for 20 minutes, and then placed in an oven at 60°C until completely dried.
[0036] b. Preparation of poly(vinylidene fluoride-trifluoroethylene) nanofibers: First, 1 gram of poly(vinylidene fluoride-trifluoroethylene) was dissolved in a mixed solution of 2 grams of N-N dimethylformamide and 2 grams of acetone , and stirred at room temperature for 2 hours until the precursor solution was homogeneous and transparent. Then, take 1 ml of precursor solution into a 5 ml disposable plastic needle to start electrospinning. Spinning parameters are: voltage 10 kV, receiving distance 10 cm.
[0037] c. Coating of nanofiber membrane: place the elastic yarn pre-stretched to 2 times the length on the collecting plate, and slowly rotate along the axial d...
Embodiment 2
[0040] Repeat Example 1, with the following differences: after the ethanol is completely volatilized in the d process, repeat the d process again according to the silver nanowire dispersion of the same concentration and the amount added, so a total of 3 times, the elastic yarn can be removed and recovered To the original length, complete the preparation process.
Embodiment 3
[0042] Repeat Example 1, with the following difference: after the ethanol is completely volatilized in the d process, repeat the d process again according to the silver nanowire dispersion of the same concentration and the amount of addition, so a total of 5 times, you can take off the elastic yarn and recover To the original length, complete the preparation process.
[0043] Embodiment 1-3 result: as figure 2 As shown, the structure of each layer can be clearly distinguished from the cross-sectional topography of the conductive fiber prepared in Example 3. image 3 Silver nanowires adsorbed on the surface of the conductive fibers and the wrinkled structure formed on the surface of the electrospun nanofibrous membrane after restoring the pre-stretching deformation. Depend on Figure 4 It can be seen that with the increase of the number of silver nanowire dispersion drops, more and more silver nanowires are deposited and adsorbed on the surface of the electrospun fiber membr...
PUM
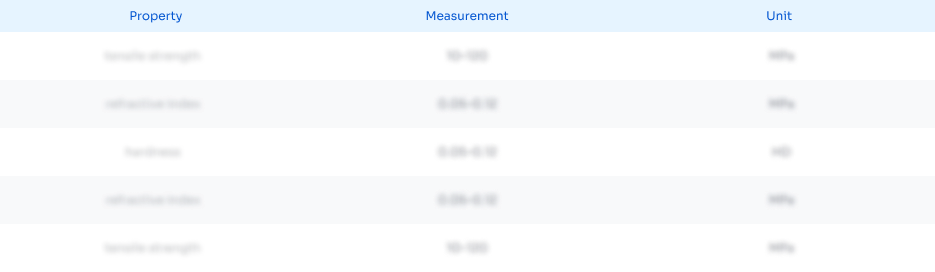
Abstract
Description
Claims
Application Information

- Generate Ideas
- Intellectual Property
- Life Sciences
- Materials
- Tech Scout
- Unparalleled Data Quality
- Higher Quality Content
- 60% Fewer Hallucinations
Browse by: Latest US Patents, China's latest patents, Technical Efficacy Thesaurus, Application Domain, Technology Topic, Popular Technical Reports.
© 2025 PatSnap. All rights reserved.Legal|Privacy policy|Modern Slavery Act Transparency Statement|Sitemap|About US| Contact US: help@patsnap.com