A method for vacuum flexible heating of curved glass
A curved glass, flexible technology, applied in the direction of ohmic resistance heating, heating element materials, ohmic resistance heating parts, etc., can solve the problem that the curved glass is difficult to achieve high-temperature coating, etc., to solve uneven heating, enhance accurate monitoring, and ensure quality Effect
- Summary
- Abstract
- Description
- Claims
- Application Information
AI Technical Summary
Problems solved by technology
Method used
Image
Examples
Embodiment approach
[0014]1) A flexible heating film is used to stick to the back of the glass to achieve seamless bonding with the glass. The suitable heating temperature range for this method is about 50-180°C;
[0015]2) A detachable flexible heating jacket is fixed on the back of the glass to achieve a good fit with the glass. Since the resistance wire used in the detachable flexible heating is wrapped with high temperature resistant glass fiber, the suitable heating temperature range for this method is about 180-350°C.
[0016]The prerequisite for implementing the vacuum heating of the present invention is to connect an external thermostat through a vacuum flange to control the above-mentioned flexible heating film or a detachable flexible heating jacket to realize temperature control. The prerequisite for the precise temperature control of the present invention is to arrange several sensors on the heated substrate to obtain the accurate temperature of the substrate.
[0017]The implementation steps of the...
Embodiment
[0025]After the curved glass piece is installed in the vacuum chamber 1, the flexible heating film or flexible heating jacket 2 is evenly attached to the back of the substrate 3. At the same time, a number of temperature sensors 4 are arranged around the substrate 3; the flexible heating film or flexible heating jacket 2 is connected to the external temperature controller 6 through the vacuum flange 5; the vacuum chamber 1 is evacuated through the vacuum pump group 7 to reach the coating site The required degree of vacuum. Such asfigure 1The shown external temperature controller heats the tightly attached flexible heating film or flexible heating jacket 2, and the temperature control is realized by the temperature controller 6. When the temperature stabilizes at the set value of 100°C, test the temperature sensors 4 arranged around the substrate 3 and find that the temperature is 96.5°C, 102.5°C, 99.4°C, 97.7°C, 99.4°C, 101.3°C, 102.3°C, basically At the set temperature of ±3.5℃, th...
PUM
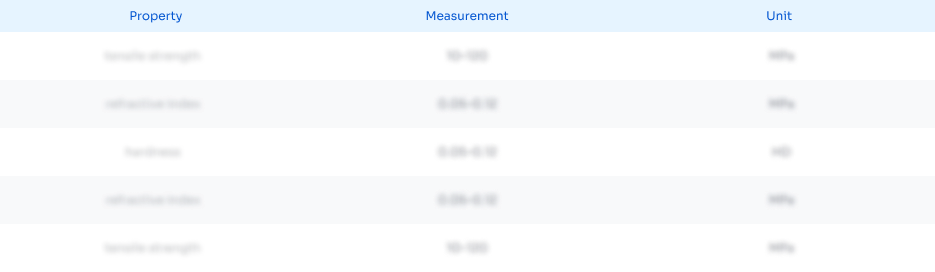
Abstract
Description
Claims
Application Information

- R&D
- Intellectual Property
- Life Sciences
- Materials
- Tech Scout
- Unparalleled Data Quality
- Higher Quality Content
- 60% Fewer Hallucinations
Browse by: Latest US Patents, China's latest patents, Technical Efficacy Thesaurus, Application Domain, Technology Topic, Popular Technical Reports.
© 2025 PatSnap. All rights reserved.Legal|Privacy policy|Modern Slavery Act Transparency Statement|Sitemap|About US| Contact US: help@patsnap.com