Preparation method of energy-saving wall material
A technology for wall materials and plastics, which is applied in the production of ceramic materials, ceramic products, clay products, etc., can solve the problems of high cost of using materials, inability to realize waste recycling, etc., to reduce weight, realize timely and effective processing, preparation handy effect
- Summary
- Abstract
- Description
- Claims
- Application Information
AI Technical Summary
Problems solved by technology
Method used
Examples
Embodiment 1
[0045] This embodiment relates to a preparation method of an energy-saving wall material;
[0046] The preparation method of the energy-saving wall material includes the following steps:
[0047] (1) Preparation of waste foam glass
[0048] Clean the waste foam glass to remove dust and oil stains on the surface, then use a single-shaft shredder to crush the waste foam glass, and pass through a 50-100 mesh sieve to obtain waste foam glass powder for future use;
[0049] (2) Preparation of industrial waste residue
[0050] Soak the inorganic waste residue produced under high temperature in shale oil industrial production in water at 40°C for 2 hours, then dry it and set it aside;
[0051] (3) Prepare raw materials according to the following ratio:
[0052] 50 parts of waste foam glass powder, 16 parts of industrial waste, 7 parts of plant straw, 13 parts of broken plastic particles, 15 parts of high-viscosity attapulgite clay, 18 parts of gypsum, 12 parts of river sand, 8 par...
Embodiment 2
[0072] This embodiment relates to a preparation method of an energy-saving wall material;
[0073] The preparation method of the energy-saving wall material includes the following steps:
[0074] (1) Preparation of waste foam glass
[0075] Clean the waste foam glass to remove dust and oil stains on the surface, then use a single-shaft shredder to crush the waste foam glass, and pass through a 50-100 mesh sieve to obtain waste foam glass powder for future use;
[0076] (2) Preparation of industrial waste residue
[0077] Soak the inorganic waste residue produced under high temperature in shale oil industrial production in water at 30°C for 3 hours, then dry it and set aside;
[0078] (3) Prepare raw materials according to the following ratio:
[0079] 40 parts of waste foam glass powder, 10 parts of industrial waste, 5 parts of plant straw, 8 parts of broken plastic particles, 10 parts of high-viscosity attapulgite clay, 15 parts of gypsum, 10 parts of river sand, 5 parts o...
Embodiment 3
[0099]This embodiment relates to a preparation method of an energy-saving wall material;
[0100] The preparation method of the energy-saving wall material includes the following steps:
[0101] (1) Preparation of waste foam glass
[0102] Clean the waste foam glass to remove dust and oil stains on the surface, then use a single-shaft shredder to crush the waste foam glass, and pass through a 50-100 mesh sieve to obtain waste foam glass powder for future use;
[0103] (2) Preparation of industrial waste residue
[0104] Soak the inorganic waste residue produced under high temperature in shale oil industrial production in water at 40°C for 3 hours, then dry it and set aside;
[0105] (3) Prepare raw materials according to the following ratio:
[0106] 50 parts of waste foam glass powder, 20 parts of industrial waste, 10 parts of plant straw, 16 parts of broken plastic particles, 17 parts of high-viscosity attapulgite clay, 23 parts of gypsum, 16 parts of river sand, 12 parts...
PUM
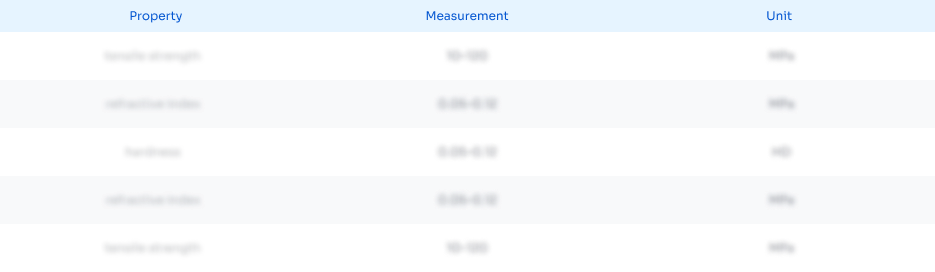
Abstract
Description
Claims
Application Information

- R&D
- Intellectual Property
- Life Sciences
- Materials
- Tech Scout
- Unparalleled Data Quality
- Higher Quality Content
- 60% Fewer Hallucinations
Browse by: Latest US Patents, China's latest patents, Technical Efficacy Thesaurus, Application Domain, Technology Topic, Popular Technical Reports.
© 2025 PatSnap. All rights reserved.Legal|Privacy policy|Modern Slavery Act Transparency Statement|Sitemap|About US| Contact US: help@patsnap.com