Automatic press-in machine for gear and drive pin
A gear-driven, press-in machine technology, used in metal processing, metal processing equipment, manufacturing tools, etc., can solve the problems of low work efficiency, difficulty in ensuring production quality, and high labor intensity, so as to ensure production quality and improve work. Efficiency and degree of automated production, the effect of reducing labor intensity and labor costs
- Summary
- Abstract
- Description
- Claims
- Application Information
AI Technical Summary
Problems solved by technology
Method used
Image
Examples
Embodiment Construction
[0022] The present invention will now be described in further detail with reference to the accompanying drawings and preferred embodiments.
[0023] A gear-driven pin automatic press-in machine, such as figure 1 , figure 2 and Figure 5 As shown, it includes a base 1 and an electric control box 2, and the base 1 is provided with a fixed plate 3 and a first feeding mechanism, a second feeding mechanism, a press-fitting mechanism 6 and The ejector mechanism 7, the electric control box 2 may include a programmable controller or a PLC controller or a single-chip microcomputer, the fixing plate 3 is horizontally fixed on the base 1 through a screw connection, and the fixing plate 3 is provided with a machining groove 32. The output ends of the first feeding mechanism and the second feeding mechanism are respectively connected to the processing groove 32. The processing groove 32 is provided with an ejection hole 33, and the pressing mechanism 6 is vertically arranged above the p...
PUM
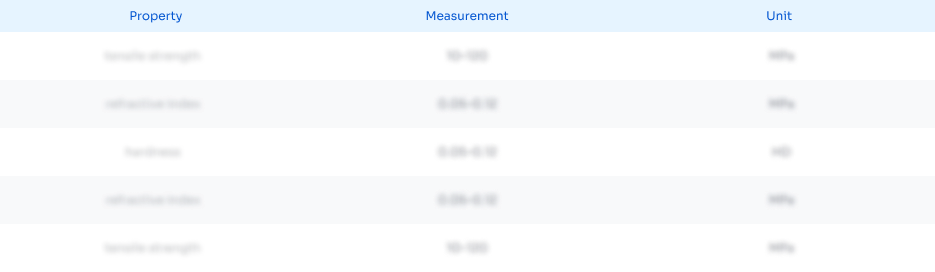
Abstract
Description
Claims
Application Information

- R&D Engineer
- R&D Manager
- IP Professional
- Industry Leading Data Capabilities
- Powerful AI technology
- Patent DNA Extraction
Browse by: Latest US Patents, China's latest patents, Technical Efficacy Thesaurus, Application Domain, Technology Topic, Popular Technical Reports.
© 2024 PatSnap. All rights reserved.Legal|Privacy policy|Modern Slavery Act Transparency Statement|Sitemap|About US| Contact US: help@patsnap.com