Modified bituminous waterproof sheet production line and production process of modified material
A waterproof membrane and modified asphalt technology, which is applied in the direction of layered products, lamination devices, lamination auxiliary operations, etc., can solve the problems of insufficient drying of waterproof membranes, unfavorable storage and transportation, accumulation, etc.
- Summary
- Abstract
- Description
- Claims
- Application Information
AI Technical Summary
Problems solved by technology
Method used
Image
Examples
Embodiment 1
[0077] see Figure 7 as shown, Figure 7 Show the production process of the modified material of embodiment one and the process flow diagram of the modified material after production when processing the waterproof coiled material; Raw material 90# asphalt is first driven into the asphalt storage tank by the pump (with a heat-conducting oil coil pipe inside) ), after the temperature rises from 90°C to 120°C, pump it into the mixing tank, then add the engine oil into the tank, heat up to 180°C, add SBS, grind and self-circulate through the colloid mill, after 0.5 hours. Continue to maintain temperature control at 185°C to 195°C for a sufficient time of 2 hours after the addition of SBS, continue to add polypropylene or polyethylene particles, maintain the temperature at 185°C to 195°C for sufficient time for 2 hours, and then put in powder. After fully stirring for 2 hours, it can be kept warm and stirred. At this time, samples can be taken for analysis. When the test result ...
Embodiment 2
[0080] see Figure 8 as shown, Figure 8 Show the production process of the modified material of embodiment two and the process flow diagram of the modified material after production when processing waterproof coiled material; Raw material 100# asphalt, at first squeezed into asphalt storage tank by pump (set heat-conducting oil pan inside tube), after the temperature rises to 90℃~120℃, pump it into the mixing tank, then add the engine oil into the tank, heat up to 185-195℃, mix the rubber powder fully for 2 hours, and then continue to keep the temperature at 185- 195°C, add polyethylene material and polypropylene granules, stir well for 2 hours, while keeping the temperature at 185-195°C, put the powder into the mixing tank. Keep the temperature controlled at 185-195°C, stir well for 2 hours, and take samples for analysis. After passing the inspection, the material can be supplied to the molding machine. That is, it is introduced into the dip coating tank 3 of the producti...
Embodiment 3
[0083] see Figure 9 as shown, Figure 9 Show the production process of the modified material of embodiment three and the process flow diagram of the modified material after production when processing the waterproof coiled material; Raw material 90# asphalt is first driven into the asphalt storage tank by the pump (with heat-conducting oil coil pipe inside) ), after the temperature rises from 90°C to 120°C, pump it into the mixing tank, then add engine oil into the tank, heat up to 180°C, add SBS and SBR, grind and self-circulate through the colloid mill, after 0.5 hours. Continue to maintain the temperature control at 185°C to 195°C, and ensure that the time is sufficient for 2 hours after the SBS is added, and then put in the powder. After fully stirring for 2 hours, it can be kept warm and stirred. At this time, samples can be taken for analysis. Keep the temperature controlled at 160-170°C. When the test result is qualified, the material can be discharged to the moldin...
PUM
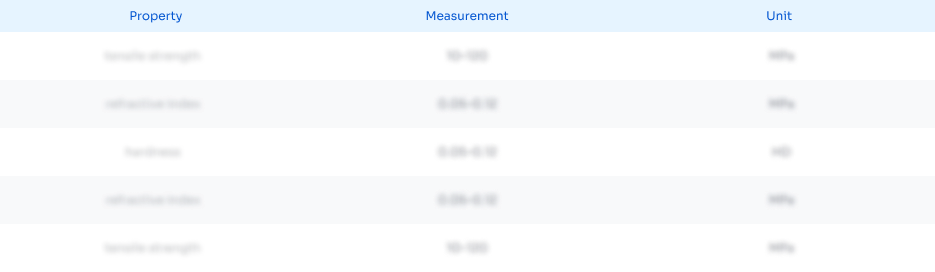
Abstract
Description
Claims
Application Information

- Generate Ideas
- Intellectual Property
- Life Sciences
- Materials
- Tech Scout
- Unparalleled Data Quality
- Higher Quality Content
- 60% Fewer Hallucinations
Browse by: Latest US Patents, China's latest patents, Technical Efficacy Thesaurus, Application Domain, Technology Topic, Popular Technical Reports.
© 2025 PatSnap. All rights reserved.Legal|Privacy policy|Modern Slavery Act Transparency Statement|Sitemap|About US| Contact US: help@patsnap.com