A multi-layer and multi-grain composite pre-packed screen suitable for sand control of silt and fine sand
A silt and fine sand, particle size technology, applied in the direction of wellbore/well components, production fluid, earthwork drilling and production, etc., can solve the problem that it is difficult to meet the sand control requirements of silty fine sand and ultra-fine sand, and it is difficult to take into account the sand retaining effect and high circulation problems such as the formation sand is easy to invade, blockage and reduce production, etc., to achieve excellent sand retaining effect, not easy to collapse and lose stability, and the effect of structural stability
- Summary
- Abstract
- Description
- Claims
- Application Information
AI Technical Summary
Problems solved by technology
Method used
Image
Examples
Embodiment 1
[0040] A multi-layer multi-grain grade composite pre-filled screen suitable for fine sand sand control, the structure is as follows Figure 1-Figure 3As shown, including the base pipe 1, there are several diversion holes 10 evenly distributed on the pipe wall of the base pipe. The diversion holes 10 are circular with a diameter of 8-10 mm. The base pipe is a central pipe with holes, which supports the filling layer and ensures the inflow of fluid.
[0041] The outer surface of the base pipe is sleeved with an inner wire winding layer 8, and the inner wire winding layer is sleeved with a multi-grain composite filling layer.
[0042] The multi-grain composite packing layer includes from the inside to the outside: the third gravel layer 4, the second gravel layer 3, and the first gravel layer 2; the third gravel layer 4 and the second gravel layer 3 pass through the secondary isolation diversion net 7 Separated, the second gravel layer 3 is separated from the first gravel layer ...
Embodiment 2
[0052] A multi-layer multi-grain grade composite pre-packed screen suitable for silt and fine sand sand control described in Example 1, the difference lies in:
[0053] In the present invention, the thickness of the third gravel layer is 10 mm, the thickness of the second gravel layer is 14 mm, and the thickness of the first gravel layer is 12 mm.
[0054] In the present invention, the median value of the gravel particle size in the third gravel layer is 1.5 times the median value of the gravel particle size in the second gravel layer; the median value of the gravel particle size in the second gravel layer is 2.0 times the median value of the gravel particle size in the first gravel layer ; The median size of the gravel in the first gravel layer is 10 times the median size of the formation sand.
[0055] In the present invention, the first-stage isolation diversion net is a stainless steel expanded net full of circular holes, with a thickness of 0.8mm; its mesh size is 2 / 3 of ...
experiment example
[0068] Experimental method: use gravel layer characteristics to evaluate the microscopic flooding simulation experimental device, and then use formation sand flooding to evaluate various performances. During the experiment, after setting the required flow rate and sand-carrying concentration and other conditions, artificially compact and fill the gravel layer into the sand filling pipe; first use clean water to carry simulated formation sand to displace the gravel layer for a long time, and measure the pressure difference on both sides of the gravel layer Then change the size of the gravel layer or filling method, and keep other conditions unchanged, repeat the experiment, measure the pressure difference on both sides of the gravel layer, the experimental pressure and flow rate; finally use the sand-retaining performance evaluation software of the gravel layer for data collection, Data processing analysis and performance evaluation index calculation of gravel layer. Through th...
PUM
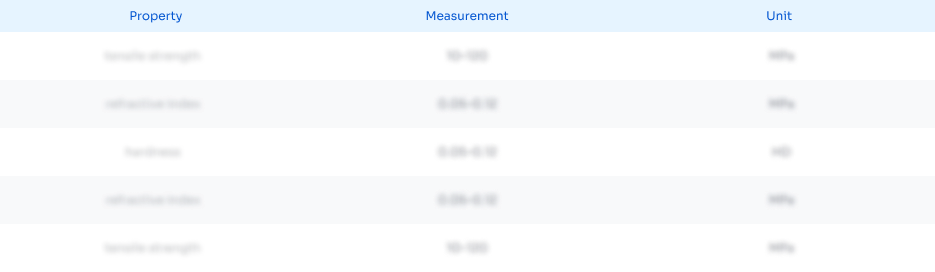
Abstract
Description
Claims
Application Information

- R&D
- Intellectual Property
- Life Sciences
- Materials
- Tech Scout
- Unparalleled Data Quality
- Higher Quality Content
- 60% Fewer Hallucinations
Browse by: Latest US Patents, China's latest patents, Technical Efficacy Thesaurus, Application Domain, Technology Topic, Popular Technical Reports.
© 2025 PatSnap. All rights reserved.Legal|Privacy policy|Modern Slavery Act Transparency Statement|Sitemap|About US| Contact US: help@patsnap.com